Causes of Coarse Grains in Castings During Production
2024-11-25 15:37:34 hits:0
Coarse grains in castings are a common but undesirable phenomenon that directly impacts the mechanical properties and service life of castings. Understanding the causes of coarse grains is crucial for optimizing production processes and improving casting quality. Based on many years of production practice and reference to relevant materials, the author will explore the possible causes of coarse grains in castings from multiple aspects.
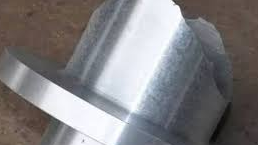
1.Impact of Alloy Composition
- Excessive Carbon Content: High carbon content in steel castings can lead to carbide precipitation, reducing nucleation rates and accelerating grain growth.
- Insufficient Alloying Elements: Trace elements like titanium and vanadium help refine grains. A lack of these elements may result in coarse grains.
- Influence of Impurities: Impurities such as sulfur and phosphorus form low-melting-point segregated zones, leading to localized grain coarsening.
2. Improper Cooling Rate Control
- Slow Cooling: A slower cooling rate provides grains with more time to grow, resulting in coarser structures.
- Uneven Cooling Gradients: Differences in cooling rates across sections can cause localized coarse grains.
- Deficient Mold Design: Uneven mold thermal conductivity or improper temperature control in molds can indirectly contribute to uneven cooling.
3. Overheating or Prolonged Melting Time
- Excessive Melting Temperature: Higher temperatures promote grain growth and may burn off trace elements, reducing nucleation sites.
- Prolonged Holding Time: Extended holding periods allow grains more time to grow, especially without sufficient stirring.
4. Other Casting Process Issues
- Excessive Mold Preheating Temperature: High preheating temperatures delay cooling, leading to coarse grains.
- Fast Pouring Speed: Rapid pouring can cause turbulence, reducing nucleation and forming coarse grain areas.
- Untreated Metallurgical Defects: Inclusions and gas porosity decrease the density of effective nucleation sites, contributing to coarser grains.
5. Lack of Grain Refinement
- Absence of Grain Refiners: Elements like boron, strontium, and manganese effectively refine grains, and their improper or lack of use can result in coarser grains.
- Insufficient Stirring: Poor distribution of refining agents or particle aggregation in the melt can impair grain refinement.
6. Improper Heat Treatment
- Excessive Annealing Temperature or Duration: Grain growth occurs during heat treatment, and over-treatment exacerbates grain coarsening.
- Uncontrolled Rapid Cooling and Slow Heating: If the cooling and heating rates are poorly controlled, grains can grow abnormally.
The causes of coarse grains involve a combination of material composition, process design, equipment, and operational practices. Addressing these issues requires careful analysis and step-by-step elimination. By controlling alloy composition, optimizing cooling rates, precisely managing melting temperatures and durations, designing better casting processes, and adopting advanced grain refinement techniques, coarse grain formation can be effectively minimized, enhancing the overall performance of castings.