How to Choose the Right Pig Iron for a Foundry?
2024-11-21 14:44:29 hits:0
Choosing the right pig iron is crucial for ensuring the quality and cost-effectiveness of castings. Below is a detailed guide to help foundries make optimal decisions when purchasing pig iron:
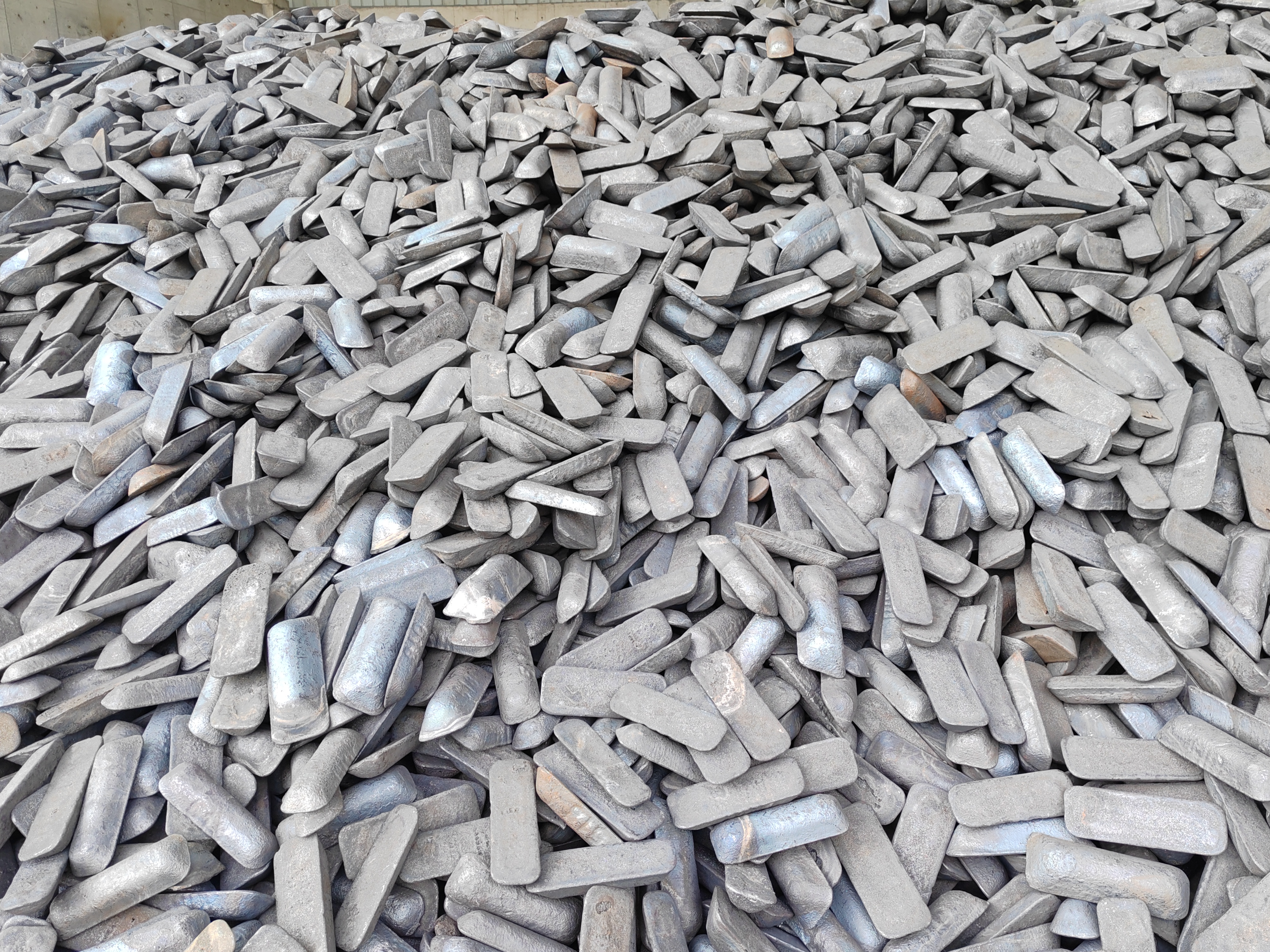
1. Define Casting Performance Requirements
Before selecting pig iron, it’s important to clarify the specific use and performance requirements of the castings. Different types of castings require different qualities of pig iron:
Mechanical Properties: Are there specific requirements for strength, hardness, or toughness?
Dimensional Accuracy: Complex shapes and high-precision castings require high-quality pig iron to improve fluidity and reduce shrinkage.
Operating Environment: Will the castings need to withstand high temperatures, corrosion, or wear?
Cost-effectiveness: Sensitivity to cost is an important consideration.
By defining these key requirements, you can narrow down the range of suitable pig iron options.
2. Main Types of Pig Iron and Their Characteristics
Select the pig iron type that meets the requirements of your castings:
Ordinary Foundry Pig Iron (Gray Cast Iron)
Applications: Suitable for mechanical parts, construction components, and other general gray cast iron products.
Characteristics:
High carbon content (3.0%-4.5%) precipitated in the form of flake graphite.
High silicon content (1.5%-3.0%) enhances fluidity and promotes graphitization.
Moderate sulfur and phosphorus content to balance strength and toughness.
Nodular Cast Iron Pig Iron
Applications: Producing high-strength and tough castings, such as pipe fittings, automotive components, and heavy machinery parts.
Characteristics:
Low sulfur (S < 0.06%) and phosphorus (P < 0.05%) levels to improve nodularization.
Typically contains magnesium and rare earth metals to form spheroidal graphite structures.
Controlled silicon content, usually 1.5%-2.5%, to avoid undesirable graphite precipitation during nodularization.
Blast Furnace Pig Iron (Coke Pig Iron)
Applications: Specialized casting needs, such as high-wear-resistance castings.
Characteristics:
Low melting point for easier melting.
Impurities (such as sulfur and phosphorus) must be carefully controlled based on requirements.
3. Detailed Chemical Composition Requirements
The chemical composition of pig iron directly affects casting performance and quality. Key parameters to monitor include:
Carbon (C)
Carbon is the primary element in pig iron, existing in the form of cementite or graphite.
Gray Cast Iron: High carbon content (>3.0%) enhances graphitization and fluidity but reduces strength if excessive.
Nodular Cast Iron: Lower carbon content (3.2%-3.6%) ensures balanced strength and toughness.
Silicon (Si)
Silicon promotes graphitization and influences hardness and shrinkage.
High Silicon Content (>2.5%): Suitable for gray cast iron, improving fluidity and machinability.
Low Silicon Content (1.5%-2.5%): Used for nodular cast iron to ensure effective nodularization.
Sulfur (S) and Phosphorus (P)
Sulfur: Harmful to casting properties, causing cold brittleness; should be controlled to <0.06%.
Phosphorus: Improves fluidity but reduces toughness; should be controlled to <0.05%.
Manganese (Mn)
Maintained at 0.5%-1.0% to enhance strength and toughness while reducing the harmful effects of sulfur.
Trace Alloying Elements
Chromium (Cr): Improves wear resistance and corrosion resistance.
Molybdenum (Mo): Enhances high-temperature strength and hardness.
4. Production Process and Furnace Material Compatibility
Melting Equipment and Process Requirements
Cupola Furnace: Suitable for batch production; select general or blast furnace pig iron while controlling volatile matter and ash content.
Electric Furnace: Ideal for high-precision castings, requiring low-impurity, high-quality pig iron.
Material Proportioning
Balance pig iron with scrap steel and return scrap to control costs while meeting performance requirements.
Gray cast iron typically uses 50%-70% pig iron, while nodular cast iron may use less pig iron but requires stricter control of sulfur and phosphorus levels.
5. Physical Appearance and Quality Inspection
When purchasing pig iron, inspect its physical condition and appearance to ensure it is suitable for melting:
Particle Size and Shape
Uniform particle size; blocky or granular pig iron melts more evenly.
Avoid excessive powder or overly large blocks, as these can reduce melting efficiency.
Surface Quality
The pig iron surface should be free of visible cracks, excessive impurities, or oxidation.
6. Supplier Selection and Certification
Supplier Credentials
Choose suppliers with a proven track record and good reputation to ensure stable supply.
Request suppliers to provide composition analysis reports and third-party certifications such as SGS reports.
Batch Testing
Before bulk purchasing, request samples for small-scale melting tests to ensure suitability for your casting process.
Logistics and Delivery Time
Choose suppliers with reliable delivery capabilities to avoid production delays caused by transportation issues.
7. Cost and Value Analysis
Cost Control
Gray Cast Iron Castings: Opt for general-grade pig iron to reduce costs.
High-performance Castings: Prioritize low-impurity, high-quality pig iron for better performance.
Comprehensive Value
Consider not only price but also factors such as composition consistency, scrap rates, and casting yield.
8. Environmental and Sustainability Considerations
Modern foundries need to consider environmental requirements:
Low Emissions
Select pig iron produced with lower carbon emissions to comply with environmental regulations.
Recycling
Prioritize pig iron with high recyclability to reduce waste.
9. Summary and Recommendations
Clear Steps: Define requirements → Screen suppliers → Obtain samples → Evaluate and test → Bulk purchase.
Adapt to Production Needs: Tailor the choice of pig iron to match melting equipment, casting specifications, and production budgets.
Ensure Quality Consistency: Work with reputable suppliers to minimize batch variability and ensure stable production.