I. What is the crankshaft?
A crankshaft is a precision-engineered mechanical component that converts reciprocating motion from engine pistons into rotational energy. As leading crankshaft manufacturers, we design these critical parts for optimal performance in automotive, marine, and industrial applications. Comprising a series of journals and counterweights, our crankshafts meet ISO 19902 standards for marine use and IATF 16949 for automotive systems.
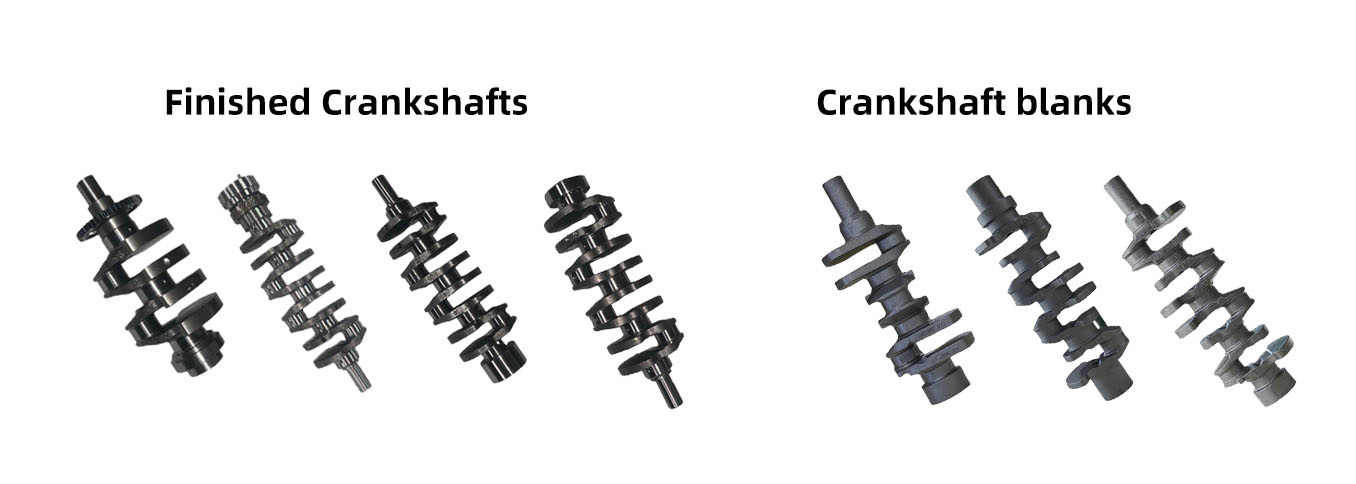
II. What does a crankshaft do?
This essential engine part performs three key functions:
Transforms linear piston movement into rotational power
Supports connecting rod bearings under extreme pressure
Maintains engine balance through strategically placed counterweights
Our custom crankshafts enhance torque delivery in ship engines crankshaft systems, reducing vibration by up to 30% compared to standard models.
III. Classification and materials of crankshaft castings?
Material Options:
Ductile Iron (QT800-6/QT900-5): Cost-effective with high tensile strength
Forged Steel: Ideal for heavy-duty applications requiring 200+ ksi yield strength
Casting Types:
Cast Crankshafts: Produced via iron mold coated sand casting for complex geometries
Forged Crankshafts: Created through hot forging processes for superior fatigue resistance
IV. What are the 4 parts of the crankshaft?
Main Journals: Support the crankshaft in engine bearings
Connecting Rod Journals: Interface with piston connecting rods
Counterweights: Balance rotational forces during operation
Flywheel Flange: Transmits power to drivetrain components
Our designs incorporate fillet rolling on journal edges, increasing fatigue life by 45%.
V. Factors Affecting Crankshaft Replacement Cost
Cost variables include:
Material Type: Forged steel costs 30-50% more than cast iron
Application Complexity: Marine crankshafts require additional corrosion protection
Customization: Precision balancing for racing engines adds 20-30% to base cost
Certifications: ISO 19902 compliance increases production costs by 15%
VI. What is the casting method of crankshaft?
Our proprietary process includes:
Induction furnace melting with 99.8% purity control
Automated iron mold coated sand casting for ±0.1mm precision
In-line spectrometer analysis every 5 minutes during production
100% ultrasonic testing for internal defects
VII. What is the difference between a camshaft and a crankshaft?
Feature | Crankshaft | Camshaft |
---|
Function | Power transmission | Valve timing |
Material | Ductile iron/forged steel | Alloy steel |
Speed | 1,000-6,000 RPM | 500-3,000 RPM |
Weight | 15-150 kg | 5-25 kg |
Maintenance | Major overhaul every 100,000 km | Routine inspection every 25,000 km |
VIII. How is a crankshaft made?
Material Selection: Choose cast iron or forged steel based on application
Precision Machining: 5-axis CNC lathes achieve ±0.01mm tolerances
Heat Treatment: Induction quenching increases surface hardness to HRC 55
Surface Finishing: Electropolishing reduces friction coefficient by 18%
Dynamic Balancing: Computer-controlled balancing to G1.0 standards
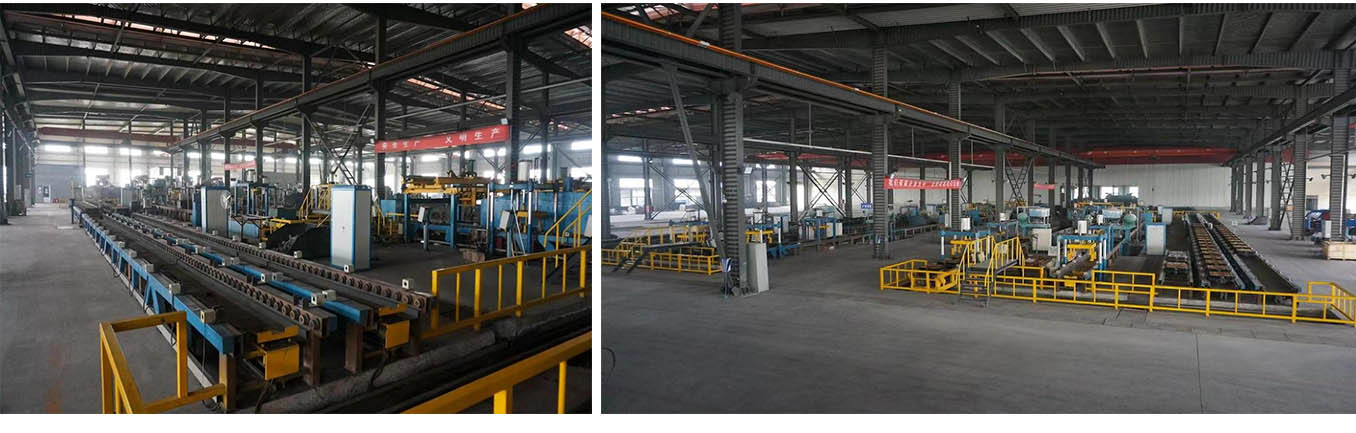
IX. Choose Tiegu for Your Customized Car Parts
As a trusted crankshaft supply company since 1998, we offer:
Custom crankshafts for Minneapolis, MN, and global markets (shipment within 15 business days)
Direct collaboration with Ohio Crankshaft Company for large-scale projects
In-house pig iron production ensuring stable crankshaft supply at 12% lower cost than competitors
0