Valve housings serve as critical components in industrial systems, directly impacting sealing, durability, and energy efficiency. With growing demands for high-precision and customized parts, valve housing machining and custom casting technologies have emerged as key solutions to optimize product performance.
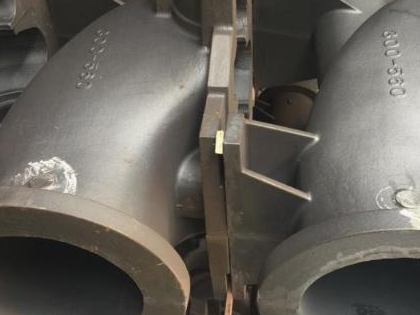
I. Core Processes in Valve Housing Machining
Valve housings are typically made from metals like cast iron, stainless steel, or aluminum. The manufacturing process combines casting and precision machining to ensure structural integrity and dimensional accuracy.
Casting Techniques: Molten metal is poured into molds to form rough shapes. Methods like sand casting and investment casting (for intricate designs) are widely used.
Precision Machining: Post-casting processes like turning, milling, and drilling refine surfaces. For example, gate valve housings require CNC machining to ensure tight seals between the gate and seat.
Surface Treatments: Electroplating, spraying, or heat treatment (e.g., quenching) enhance corrosion and wear resistance. Surfacing with stainless steel welds can protect against erosion.
II. Advantages of Custom Casting
Custom casting allows tailored material selection, structural optimization, and functional integration:
Material Flexibility: Choose materials like ductile iron or special alloys based on media (e.g., corrosive fluids, high-temperature gases).
Structural Design: Finite Element Analysis (FEA) optimizes wall thickness and ribs for pressure resistance. Integral casting reduces welding risks in high-pressure applications.
Functional Integration: Pre-installed sensor interfaces or mounting accessories simplify assembly.
Applications:
Energy: Hydroelectric valve housings with fatigue-resistant designs.
Chemicals: Corrosion-resistant alloy castings for aggressive media.
Automotive: Lightweight aluminum castings for EGR valve housings.
III. Customization Workflow & Technical Challenges
Requirement Analysis: Engineers review drawings or specifications (pressure ratings, media type).
Tooling Design: CAD/CAM technology creates prototypes and molds.
Quality Assurance: X-ray inspection and 3D coordinate measurement ensure defect-free parts.
Post-Processing: Surface finishing, coating, or assembly as needed.
Challenges & Solutions:
Complex Geometries: 3D-printed sand molds accelerate prototyping.
Material Uniformity: Optimized cooling rates reduce shrinkage defects.
Cost Efficiency: Standardized processes lower unit costs for bulk orders.
IV. Choosing a Reliable Manufacturer
Technical Expertise: Look for multi-material casting, CNC machining, and advanced testing capabilities.
Industry Experience: Evaluate past projects in automotive, energy, and other sectors.
Certifications: Ensure compliance with ISO 9001, ASME, or other international standards.
By leveraging valve housing machining and custom casting, businesses can streamline production from prototyping to mass manufacturing, while reducing maintenance costs and extending equipment lifespans.