In high-pressure environments such as petrochemical, water conservancy, and energy extraction, the safety of pipeline systems directly impacts production efficiency and personnel safety. Ductile iron pipe fittings have emerged as the preferred solution in high-pressure scenarios due to their superior mechanical properties and corrosion resistance. This article delves into the core advantages of ductile iron fittings in high-pressure environments, providing scientific selection and application guidance through real-case data.
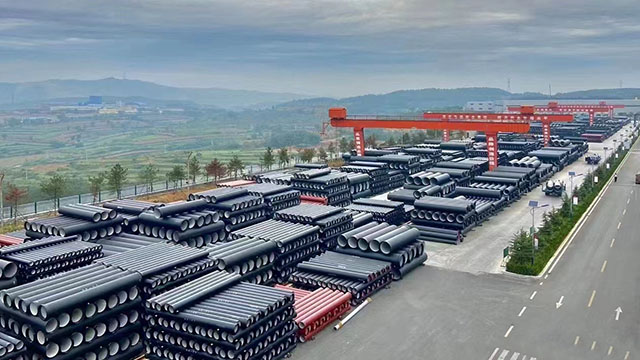
Types of High-Pressure Fittings for Ductile Iron Pipes
In high-pressure systems, the types of ductile iron fittings directly impact pipeline safety and functionality. Here are common high-pressure fittings and their features:
2.1 Elbows
Function: Alter fluid flow direction to adapt to complex pipeline layouts.
Pressure Rating: Typically ranging from PN16 to PN100 (16 bar to 100 bar).
Applications: Connecting high-pressure reactors in petrochemical refineries, redirecting water pipelines in hydropower stations.
Advantages: The curved radius design of ductile iron elbows minimizes turbulence and reduces pressure loss.
2.2 Tees
Function: Enable connections between main and branch pipelines to distribute fluid flow.
Pressure Rating: Similar to elbows, supporting high-pressure branching requirements.
Applications: Multi-production line water supply in chemical plants, urban high-pressure fire systems.
Material Innovation: Some tees feature epoxy resin linings to enhance corrosion resistance.
2.3 Flanges
Function: Provide detachable connections via bolts for easy maintenance and repairs.
Pressure Rating: Up to Class 600 (approximately 100 bar).
Applications: High-pressure oil pipelines on offshore drilling platforms, steam systems in thermal power plants.
Sealing Technology: Paired with spiral-wound metal gaskets to ensure zero leaks under high pressure.
Key Factors to Consider When Choosing High-Pressure Fittings
In high-pressure environments, fitting selection must balance multiple factors to ensure long-term system stability:
3.1 Material Strength and Corrosion Resistance
Ductile Iron Advantages: Tensile strength exceeding 400 MPa and elongation of 10%, far surpassing ordinary cast iron (≈200 MPa tensile strength).
Environmental Adaptability: For corrosive media like hydrogen sulfide or chloride ions, choose fittings with epoxy or polyurethane linings (e.g., corrosion-resistant high-pressure fitting series).
Case Data: After using coated fittings in an offshore oilfield, the corrosion rate dropped from 0.2 mm/year to 0.05 mm/year.
3.2 Sealing Technology
Metal vs. Rubber Seals: Spiral-wound metal gaskets (e.g., metal gasket products) withstand temperatures up to 300℃, while EPDM rubber suits liquids from -40℃ to 120℃.
Leakage Test Standards: Fittings compliant with ISO 15848-1 have a leakage rate <5×10⁻⁵ mbar·L/s.
Design Innovation: Some fittings feature dual-seal structures with secondary sealing grooves for enhanced safety.
3.3 Installation Ease and Long-Term Reliability
Quick-Connect Technology: Mechanical fittings (e.g., quick-connect flange series) reduce installation time by 50%.
Fatigue Life: Fittings tested for 1 million pressure cycles ensure over 20 years of service.
Maintenance Cost: Modular designs allow repairs without replacing entire pipelines.
Case Studies: High-Pressure Systems Enhanced by Ductile Iron Fittings
Here are two real-world examples demonstrating the effectiveness of ductile iron fittings in high-pressure applications:
4.1 Petrochemical Plant Upgrade
Challenge: A refinery’s catalytic cracking unit needed to increase operating pressure to 250 bar, but carbon steel fittings suffered frequent leaks, costing $800,000 annually in maintenance.
Solution: Custom ductile iron elbows and flanges with polyurethane linings, rated for Class 900 (150 bar).
Results:
90% reduction in leaks, maintenance costs dropped to $80,000/year.
System uptime increased from 4,000 to 7,200 hours/year.
Data Comparison:
Metric | Carbon Steel Fittings | Ductile Iron Fittings |
---|
Max Pressure | 180 bar | 250 bar |
Corrosion Rate | 0.3 mm/year | 0.03 mm/year |
Life-Cycle Cost | $3.2M | $1.5M |
4.2 Hydropower Station Pipeline
Challenge: A hydropower station’s water diversion pipeline suffered frequent fitting fractures due to pressure fluctuations, threatening downstream safety.
Solution: Ductile iron tees and reducers paired with smart pressure sensors (e.g., intelligent fitting monitoring system).
Results:
Pressure fluctuations reduced from ±30 bar to ±5 bar, enhancing system stability.
Predictive maintenance avoided potential $2M in equipment damage.
Technical Highlights:
Fittings comply with ASME B31.1 power piping standards.
Sensors monitor pressure in real time, enabling fault alerts via the remote management platform.
Maintenance and Long-Term Safety Tips
Regular maintenance of high-pressure fittings is critical for long-term system safety. Here are key tips for ductile iron fitting maintenance:
5.1 Preventive Maintenance Schedule
Annual Inspections:
Quarterly Cleaning:
5.2 Advanced Monitoring Technologies
5.3 Emergency Response Protocol
Leak Handling Steps:
Immediately close upstream valves to cut off fluid supply.
Use leak clamps (e.g., high-pressure leak repair kit) for temporary sealing.
Contact professional teams for repairs (service inquiry: emergency repair services).
Spare Parts Management:
Conclusion & Call to Action
In high-pressure environments, the selection of ductile iron pipe fittings directly impacts system safety, efficiency, and costs. Through this analysis, we’ve highlighted three key factors for high-pressure fitting selection: material strength, sealing technology, and maintenance. Ductile iron’s superior mechanical properties and corrosion resistance make it the ideal choice for industries like oil, chemicals, and water conservancy.
Take action today to optimize your high-pressure system!