Gravity Die Casting vs Pressure Die Casting: A Comprehensive Comparison
2025-02-10 10:21:05 hits:0
In the vast realm of metal casting, gravity die casting and pressure die casting stand as two prominent techniques, each with its own set of unique attributes that determine their applications across diverse industries. A detailed understanding of their differences is crucial for manufacturers aiming to optimize production processes and product quality.
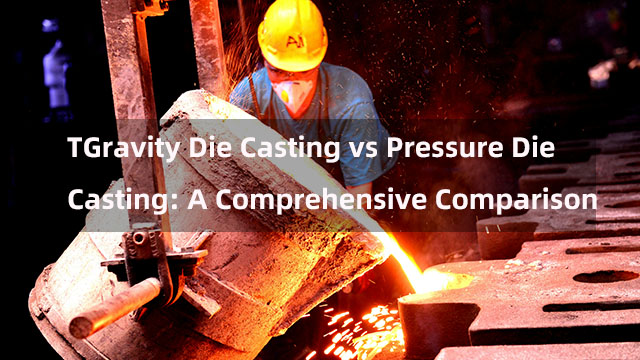
1. Fundamental Principles
1.1 Gravity Die Casting
Gravity die casting, as the name implies, hinges on the force of gravity for its operation. The process begins with preheating a die cavity, which is typically made of metal, to a specific temperature. Once preheated, the molten metal, which could be aluminum, copper, or certain ferrous alloys, is carefully poured into the cavity. Gravity then takes over, gently guiding the metal to fill every nook and cranny of the die. As the metal cools and solidifies within the cavity, it assumes the shape of the die, resulting in the formation of the desired casting. This method offers a relatively simple and straightforward approach to metal casting, relying on a natural force that has been harnessed for centuries in the art of metal shaping.
1.2 Pressure Die Casting
Pressure die casting, in contrast, operates on a different principle. Instead of relying solely on gravity, this technique employs external pressure to propel the molten metal into the die cavity. This is achieved through the use of mechanical devices such as a piston or a plunger. The high - pressure force ensures that the molten metal is injected into the cavity at a rapid pace. This not only allows for quick filling but also enables the metal to reach even the most intricate and detailed sections of the die, which might be challenging to fill under the influence of gravity alone.
2. Process Characteristics
2.1 Gravity Die Casting
One of the notable characteristics of gravity die casting is its relatively slow filling speed. While this can be an advantage in some cases, as it allows for a more controlled and natural filling process, it also has its drawbacks. The slow filling rate may lead to the entrapment of air and the formation of porosity within the casting, especially when dealing with complex geometries. Additionally, the presence of inclusions can be more common in gravity - die - cast parts. However, the simplicity of the process is a major plus. It does not demand highly specialized or high - pressure equipment, making it a cost - effective option for small - to - medium - scale production runs. Manufacturers can set up a gravity die casting operation with relatively less capital investment in equipment, making it accessible to a wider range of enterprises.
2.2 Pressure Die Casting
Pressure die casting is renowned for its high filling speed. The application of external pressure enables the molten metal to be forced into the die cavity in a matter of seconds. This rapid filling is particularly beneficial for producing complex and thin - walled parts. The high - pressure environment also helps in reducing porosity significantly. As the metal is compacted under pressure, the density of the casting increases, leading to improved mechanical properties. However, this process comes with a higher price tag. The need for sophisticated high - pressure equipment, along with the associated maintenance and operational costs, makes pressure die casting more suitable for large - scale mass production. The initial investment in pressure die casting machinery can be substantial, but the economies of scale achieved in high - volume production can offset these costs.
3. Part Quality
3.1 Gravity Die Casting
Castings produced through gravity die casting often exhibit a relatively coarse grain structure. This is a consequence of the slower cooling rate and the natural filling process. The coarse grain structure can have an impact on the mechanical properties of the parts. For example, the tensile strength and hardness of gravity - die - cast parts may be lower compared to those produced by pressure die casting. Additionally, the surface finish of gravity - die - cast components is generally less smooth. The slower filling and the potential for air entrapment can result in a surface that may have minor imperfections, which might require additional finishing operations if a high - quality surface is desired.
3.2 Pressure Die Casting
Pressure die casting excels in producing parts with a fine - grained structure. The high - pressure filling and the rapid cooling that often accompanies it lead to a more refined microstructure. This, in turn, contributes to better mechanical properties. Parts produced by pressure die casting typically have higher strength, hardness, and fatigue resistance. The surface finish of these parts is also superior, with a smoother and more uniform appearance. The high - pressure injection ensures that the molten metal adheres closely to the die walls, resulting in a part that closely mimics the precision of the die cavity. This makes pressure - die - cast parts highly suitable for applications where aesthetics and high - performance requirements go hand in hand.
4. Material Selection
4.1 Gravity Die Casting
Gravity die casting is versatile in terms of material selection. It can accommodate a wide range of metals, including aluminum, copper, and some ferrous alloys. Materials with good fluidity are particularly well - suited for this process. For instance, certain aluminum alloys with low viscosity in their molten state can flow easily under the influence of gravity into the die cavity, ensuring a complete and uniform filling. This makes gravity die casting a viable option for manufacturers working with different types of metals and alloys, depending on the specific requirements of the end - product.
4.2 Pressure Die Casting
Pressure die casting is predominantly used with non - ferrous alloys, with aluminum and zinc alloys being the most common choices. These alloys exhibit excellent fluidity and castability under pressure. The ability of aluminum and zinc alloys to flow freely when forced under high - pressure conditions allows for the production of complex shapes with high precision. Their relatively low melting points also make them easier to handle in the molten state during the pressure die casting process. Additionally, the mechanical properties of these non - ferrous alloys, such as their light weight and good corrosion resistance, further enhance their suitability for applications in industries like automotive, aerospace, and electronics.
5. Application Fields
5.1 Gravity Die Casting
Gravity die casting finds its niche in applications where high precision and top - tier performance are not the primary requirements. It is commonly used in the production of general mechanical parts, such as brackets, housings, and some simple automotive components that do not demand the highest levels of strength and durability. In the household appliance industry, gravity die casting is often employed to manufacture parts like the bases of small appliances or some internal components where cost - effectiveness and basic functionality are more important than extreme performance.
5.2 Pressure Die Casting
Pressure die casting has carved out a significant role in high - tech and high - performance industries. In the automotive industry, it is extensively used for producing engine blocks, transmission cases, and other critical components. These parts need to have high strength, precision, and reliability to withstand the demanding operating conditions of an automobile. In the aerospace sector, pressure die casting is utilized to create lightweight yet high - strength parts that are essential for aircraft and spacecraft. The electronics industry also benefits from pressure die casting, using it to produce the shells and components of electronic devices, where both aesthetics and functionality are crucial.
In conclusion, gravity die casting and pressure die casting are two distinct yet equally important techniques in the metal casting domain. Each method has its own set of strengths and weaknesses, and the choice between them depends on a multitude of factors, including the nature of the product, production volume, cost constraints, and material requirements. By carefully evaluating these factors, manufacturers can make an informed decision and select the casting method that best suits their specific needs, thereby optimizing production efficiency and product quality.