Usual Manufacturing Defects in High Pressure Die Casting
2025-02-10 10:28:01 hits:0
High - pressure die casting is a widely adopted manufacturing process in various industries due to its ability to produce complex - shaped, high - precision parts with excellent mechanical properties. However, like any manufacturing technique, it is not without its challenges. There are several common manufacturing defects that can occur during high - pressure die casting, which can significantly impact the quality and functionality of the final products. Understanding these defects, their causes, and how to mitigate them is crucial for manufacturers aiming to maintain high - quality production.
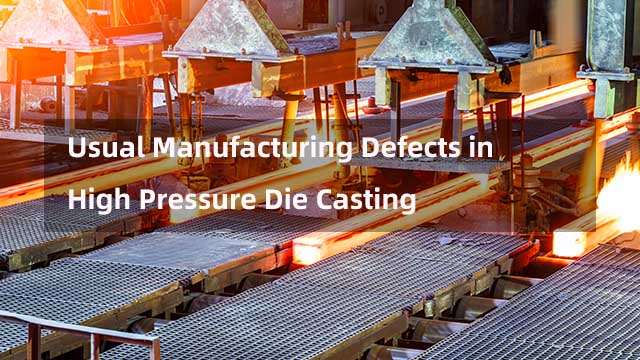
1. Porosity
1.1 Gas Porosity
Gas porosity is one of the most prevalent defects in high - pressure die casting. It is mainly caused by the entrapment of air or other gases during the filling process. When the molten metal is injected into the die cavity at high speed, air pockets can be trapped within the metal. Additionally, gases can also be released from the die lubricants or the decomposition of organic materials in the die. The presence of gas porosity can reduce the density and mechanical strength of the casting. For example, in the production of automotive engine components, gas - porous castings may lead to reduced engine performance and potential failure under high - stress conditions.
To prevent gas porosity, proper venting of the die is essential. Dies should be designed with well - placed vents to allow the escape of air and gases during the filling process. Using high - quality die lubricants that produce minimal gas emissions can also help. Moreover, controlling the injection speed and pressure can optimize the filling process and reduce the likelihood of air entrapment.
1.2 Shrinkage Porosity
Shrinkage porosity occurs as the molten metal cools and solidifies. Metal shrinks during the solidification process, and if there is insufficient molten metal to compensate for this shrinkage, voids or pores will form. Thick - walled sections of the casting are more prone to shrinkage porosity because they cool more slowly. In the manufacturing of large - scale industrial parts, such as hydraulic cylinder bodies, shrinkage porosity can lead to leaks and reduced functionality.
To address shrinkage porosity, techniques like riser design can be employed. Risers are additional reservoirs of molten metal that are connected to the casting. They provide a source of metal to feed the casting during solidification, compensating for the shrinkage. Proper gating systems, which control the flow of molten metal into the die, can also help ensure that the casting is filled uniformly and that there is enough metal to account for shrinkage.
2. Surface Defects
2.1 Cold Shuts
Cold shuts are surface defects that appear as a visible line or seam on the surface of the casting. They occur when two streams of molten metal meet but do not fuse properly. This can happen when the injection speed is too low, or the temperature of the molten metal is too low. In the production of decorative metal parts, cold shuts can be a major aesthetic issue, rendering the product unfit for sale.
To avoid cold shuts, increasing the injection speed and ensuring that the molten metal is at the appropriate temperature are key. Preheating the die to an optimal temperature can also improve the flow and fusion of the molten metal. Additionally, optimizing the gating system to ensure a smooth and consistent flow of metal into the die can help prevent cold shuts.
2.2 Flash
Flash is another common surface defect in high - pressure die casting. It is the thin, excess material that forms around the edges of the casting where the die halves meet. Flash is typically caused by excessive injection pressure, worn - out die components, or improper die alignment. In the manufacturing of electronic device housings, flash can interfere with the proper fit of components and affect the overall appearance of the product.
To reduce flash, it is important to maintain the die in good condition. Regular inspection and replacement of worn - out die components, such as die - closing mechanisms and seals, can prevent flash formation. Adjusting the injection pressure to an appropriate level and ensuring accurate die alignment are also crucial steps in minimizing flash.
3. Dimensional Deviations
3.1 Over - dimension or Under - dimension
Dimensional deviations, including over - dimension and under - dimension of the casting, can occur due to several factors. The thermal expansion and contraction of the die and the molten metal during the casting process can lead to dimensional changes. If the die design does not account for these thermal effects, the final casting may not meet the required dimensions. In the aerospace industry, where precision is critical, even small dimensional deviations can render parts unusable.
To control dimensional deviations, accurate die design is essential. Designers need to consider the thermal expansion coefficients of the die material and the molten metal and make appropriate allowances in the die dimensions. Additionally, precise control of the casting process parameters, such as temperature, pressure, and cooling rate, can help minimize dimensional variations.
3.2 Warping
Warping is a form of dimensional deviation where the casting becomes distorted from its intended shape. It is often caused by uneven cooling rates within the casting. Thick and thin sections of the casting cool at different speeds, creating internal stresses that can cause the part to warp. In the production of large - scale sheet - metal - like castings, warping can be a significant problem, affecting the fit and functionality of the part.
To prevent warping, proper cooling strategies are necessary. This may involve using cooling channels in the die to ensure more uniform cooling of the casting. Optimizing the part design to reduce the difference in wall thicknesses can also help minimize internal stresses and prevent warping.
In conclusion, while high - pressure die casting offers numerous advantages in manufacturing, the presence of common defects such as porosity, surface defects, and dimensional deviations can pose challenges. By understanding the causes of these defects and implementing appropriate preventive measures, manufacturers can improve the quality of their high - pressure die - cast products, reduce waste, and enhance their competitiveness in the market.
As a leading player in the industry, Tiegu has accumulated rich experience in the field of high - pressure die casting. Tiegu has a professional technical team that can precisely control various parameters in the die - casting process and effectively prevent the occurrence of various common defects. When dealing with the problem of gas porosity, Tiegu has greatly reduced the probability of gas porosity by optimizing the die venting system and cooperating with self - developed low - gas - emission lubricants. Regarding shrinkage porosity, Tiegu uses advanced simulation software to accurately analyze the metal solidification process, and thus designs the most reasonable riser and gating systems. In terms of solving surface defects and dimensional deviations, Tiegu utilizes high - precision die - processing equipment and strict quality inspection processes to ensure that every die - cast product can meet high - quality standards. Choosing Tiegu means choosing a high - quality and highly reliable high - pressure die - casting solution to escort your product production.