Gray and Ductile Iron Casting: An In - Depth Exploration
2025-02-10 10:41:16 hits:0
In the realm of metal casting, gray iron casting and ductile iron casting hold significant positions, each with its own unique characteristics, production processes, and application scopes. Understanding the differences and similarities between them is crucial for manufacturers to make informed decisions in material selection and production planning.
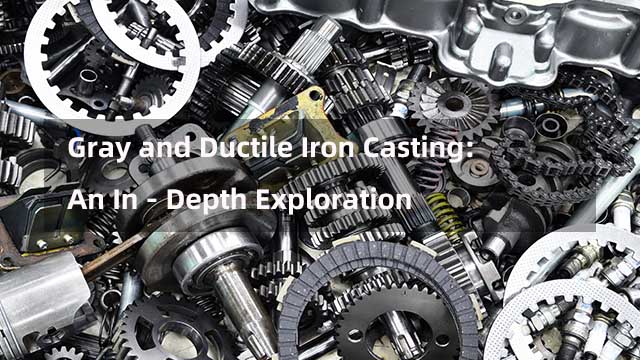
1. Fundamental Characteristics
1.1 Gray Iron Casting
Gray iron gets its name from the grayish - black appearance of its fracture surface, which is mainly due to the presence of graphite flakes. In gray iron, carbon exists in the form of graphite flakes dispersed throughout the iron matrix. These graphite flakes act as stress raisers to some extent, but they also contribute to certain properties of gray iron. For example, gray iron has excellent damping capacity, which makes it suitable for applications where vibration absorption is required. It also has good machinability because the graphite flakes can act as internal lubricants during the machining process, reducing tool wear. However, the presence of graphite flakes weakens the continuity of the iron matrix, resulting in relatively low tensile strength and ductility compared to some other types of cast iron.
1.2 Ductile Iron Casting
Ductile iron, also known as nodular iron, is characterized by the presence of graphite nodules instead of flakes. The graphite in ductile iron is in a spherical or nodular form, which is achieved through a special inoculation treatment during the casting process. This unique graphite morphology has a profound impact on the mechanical properties of ductile iron. The spherical graphite nodules do not act as strong stress raisers as the flakes in gray iron do. As a result, ductile iron has much higher tensile strength, elongation, and toughness compared to gray iron. It can withstand significant plastic deformation before failure, making it suitable for applications that require high - strength and impact - resistant materials.
2. Casting Processes
2.1 Gray Iron Casting Process
The casting process for gray iron is relatively straightforward. First, the raw materials, including iron, carbon, silicon, and other alloying elements, are melted in a furnace. Once the molten metal reaches the appropriate temperature and chemical composition, it is poured into a pre - heated mold. The mold can be made of various materials such as sand, metal, or a combination of both, depending on the complexity and quantity of the castings. After pouring, the molten metal cools and solidifies in the mold, taking on the shape of the mold cavity. Once solidified, the casting is removed from the mold and may undergo post - processing operations such as machining, heat treatment, and surface finishing.
2.2 Ductile Iron Casting Process
The ductile iron casting process has some additional steps compared to gray iron casting. After melting the raw materials, a nodulizing agent, usually magnesium - based, is added to the molten iron. This nodulizing agent transforms the graphite from a flake - like structure to a nodular one. Then, an inoculant is added to further refine the graphite nodules and improve the overall quality of the casting. The molten metal is then poured into the mold, and the subsequent solidification and post - processing steps are similar to those of gray iron casting. However, the quality control during the ductile iron casting process is more stringent due to the sensitivity of the nodularization process to factors such as temperature, chemical composition, and the addition rate of the nodulizing and inoculating agents.
3. Performance Differences
3.1 Mechanical Properties
As mentioned earlier, ductile iron clearly outperforms gray iron in terms of mechanical properties. The tensile strength of gray iron typically ranges from 100 - 300 MPa, while that of ductile iron can reach 400 - 1000 MPa or even higher, depending on the specific grade and heat treatment. The elongation of gray iron is usually very low, often less than 1%, while ductile iron can have an elongation of 2 - 20% or more. The higher strength and ductility of ductile iron make it suitable for applications where gray iron would fail, such as in the manufacturing of crankshafts, suspension components in the automotive industry, and large - diameter pipes in the water and gas transportation industries.
3.2 Thermal and Damping Properties
Gray iron has better thermal conductivity than ductile iron, which makes it a better choice for applications where heat dissipation is important, such as in engine cylinder blocks. On the other hand, gray iron's excellent damping capacity is unrivaled by ductile iron. This makes gray iron ideal for use in machine tool bases, where vibration absorption is crucial to ensure the accuracy of machining operations.
4. Application Fields
4.1 Applications of Gray Iron Casting
Gray iron is widely used in the automotive industry for components such as engine cylinder blocks, cylinder heads, and brake drums. In the machinery industry, it is used for manufacturing machine tool bases, housings, and flywheels. The excellent damping and machinability of gray iron make it a preferred material for these applications. In addition, gray iron is also used in the production of some household appliances, such as the bases of washing machines and dryers, due to its cost - effectiveness and basic mechanical properties.
4.2 Applications of Ductile Iron Casting
Ductile iron is extensively used in the automotive industry for high - strength components like crankshafts, camshafts, and suspension arms. In the construction industry, it is used for manufacturing pipes, fittings, and manhole covers. The high strength, toughness, and corrosion resistance of ductile iron make it suitable for these applications. In the mining industry, ductile iron is used to make various mining equipment components that need to withstand harsh operating conditions, such as crushers and conveyors.
In conclusion, gray iron casting and ductile iron casting are two important casting processes with distinct characteristics. While gray iron is favored for its damping, machinability, and heat - dissipation properties, ductile iron stands out for its high strength, ductility, and toughness. The choice between them depends on the specific requirements of the application, including mechanical properties, cost, and production volume. As the manufacturing industry continues to evolve, both gray iron and ductile iron casting will continue to play important roles in meeting the diverse needs of different industries.