Energy Consumption: Green Casting vs Traditional Casting
2025-01-24 10:25:11 hits:0
In the current booming manufacturing industry, casting, as an important basic process, has a non - negligible energy consumption. With the enhancement of environmental awareness and the deepening of the concept of sustainable development, green casting has gradually become the focus of the industry. Conducting a comparative analysis of the energy consumption between green casting and traditional casting helps to clearly understand the advantages of green casting in energy utilization and promote the energy - saving transformation of the casting industry.
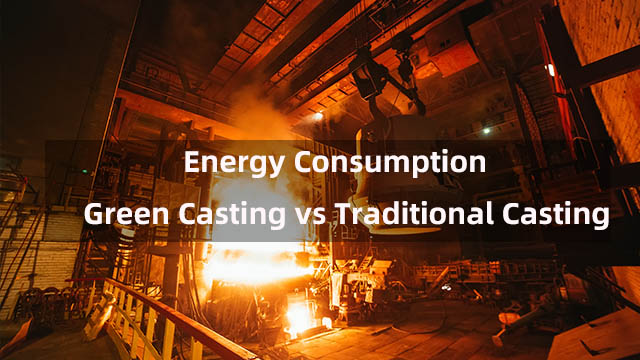
Energy Consumption Comparison in the Melting Process
In the casting process, melting is a key step to heat metal raw materials to a liquid state, and it consumes a high amount of energy. Traditional casting often uses equipment such as resistance furnaces and cupola furnaces for melting. Taking the cupola furnace as an example, it needs to consume a large amount of coke to provide heat during the melting process. Not only is its thermal efficiency relatively low, generally around 30% - 40%, but also in order to ensure the continuous progress of the reaction in the furnace, fuel needs to be continuously replenished. According to statistics, for the production of 1 ton of ordinary cast iron parts, the energy consumption of melting using a cupola furnace is approximately 500 - 600 kg of standard coal.
Green casting actively adopts advanced technologies in the melting process, such as medium - frequency induction furnaces. This kind of equipment heats metals using the principle of electromagnetic induction, and its thermal efficiency can be as high as 60% - 70%. By precisely controlling the electromagnetic frequency and current magnitude, the metal can be quickly heated to the required temperature, and the heating process is relatively uniform, reducing the ineffective loss of energy. Similarly, for the production of 1 ton of ordinary cast iron parts, the energy consumption of melting using a medium - frequency induction furnace can be reduced to 300 - 400 kg of standard coal. Compared with the traditional cupola furnace, the energy consumption is reduced by about 20% - 30%.
Energy Consumption Comparison in the Molding Process
Molding is a process that provides a forming space for the molten metal. The molding process of traditional casting mostly relies on manual or semi - automated equipment, and a large number of non - renewable organic binders and drying equipment are used. For example, in sand casting, the traditional clay sand molding requires long - time sand mixing and compaction operations, consuming a large amount of manpower and electricity. At the same time, in order to make the sand mold reach a certain strength, it needs to be dried. The energy consumption of the drying equipment is relatively high, especially for large - sized sand molds, and one drying may consume hundreds of kilowatt - hours of electricity.
Green casting has made many innovations in the molding process. On the one hand, new molding materials such as self - hardening sand are used. These materials have good fluidity and curing properties and can quickly harden and form at room temperature without additional drying processes, greatly saving energy. On the other hand, more automated molding equipment, such as static pressure molding machines, is utilized. It can accurately control the compactness and dimensional accuracy of the sand mold, not only improving production efficiency but also, due to the stable operation of the equipment, having relatively low energy consumption. It is estimated that under the same production output, the energy consumption of the molding process in green casting can be reduced by 30% - 40% compared with traditional casting.
Energy Consumption Comparison in the Heat - Treatment Process
Heat treatment is an important means to improve the performance of castings, but it is also a process with high energy consumption. The heat - treatment processes of traditional casting, such as quenching and tempering, often require heating the castings to a relatively high temperature and maintaining it for a long time to achieve microstructure transformation and performance optimization. Due to the limited thermal efficiency of the heating equipment and a large amount of heat dissipating into the surrounding environment during the heating process, the energy consumption is relatively high. For example, for a batch of automotive engine cylinder blocks undergoing traditional heat treatment, the energy consumption per furnace treatment may reach thousands of kilowatt - hours.
Green casting has introduced advanced control technologies and energy - saving equipment in the heat - treatment process. Vacuum heat - treatment technology is adopted, which can heat the castings in a low - pressure environment, reducing oxidation and decarburization phenomena and improving the quality of the castings. At the same time, due to the different heat - conduction properties of the vacuum environment from the atmospheric environment, the energy required for heating can be effectively reduced. In addition, an intelligent temperature control system is used, which can accurately control the heating rate, holding time, and cooling rate according to the material, size, and heat - treatment requirements of the castings, avoiding excessive energy consumption. Practice has shown that the energy consumption of the heat - treatment process in green casting can be reduced by 20% - 50% compared with traditional casting.
From the comparison of energy consumption in the main processes such as melting, molding, and heat treatment, it can be seen that green casting, with its advanced technologies and processes, is significantly superior to traditional casting in energy - utilization efficiency. Reducing energy consumption not only helps casting enterprises reduce production costs but also reduces the negative impact on the environment, which is in line with the strategic requirements of sustainable development. With the continuous development and improvement of green - casting technologies, it is expected to become the mainstream production mode in the casting industry in the future and promote the entire industry to move towards a more energy - saving and environmentally friendly direction.
As an active explorer in the industry, Tiegu has been committed to the research and application of green - casting technologies. In terms of energy - consumption control, Tiegu has reduced energy consumption in all aspects by introducing advanced green - casting equipment and optimizing the production process. Compared with traditional casting methods, the green - casting process adopted by Tiegu has achieved an overall energy - consumption reduction of more than 30%. While enhancing its own competitiveness, it has also set a good example of energy conservation and emission reduction for the industry. Tiegu looks forward to working hand in hand with more enterprises to jointly promote the popularization of green - casting technologies in the industry and contribute to the green transformation of the casting industry.
Previous: 3D printing helps green casting