Which Parts Are Suitable for Gravity Casting?
2025-01-23 09:15:52 hits:0
In modern manufacturing, gravity casting plays a crucial role in the production of numerous parts with its unique technological characteristics. Understanding which parts are suitable for gravity casting is of great significance for enterprises to optimize production processes, reduce costs, and improve product quality.
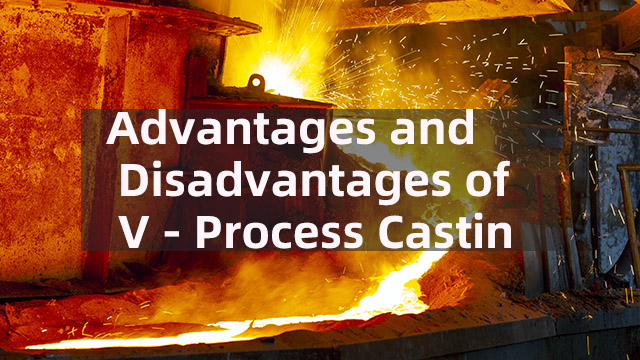
1. Parts in the Automotive Industry
1.1 Engine Blocks
The engine block is the core component of an automotive engine, featuring a complex structure with multiple internal cavities and water channels. Gravity casting can meet the requirements for complex shapes. The liquid metal evenly fills the mold cavity under the action of gravity, forming a complete and uniformly wall - thicknessed block. Many automotive brands such as Toyota and Honda often use the gravity casting process for their engine blocks, with a huge annual output, strongly ensuring the stable supply of automotive production.
1.2 Cylinder Heads
Cylinder heads also have a complex structure, with intake ports, exhaust ports, spark plug mounting holes, etc. distributed on them. Gravity casting can ensure that the liquid metal precisely fills each small passage and hole position under the action of gravity, producing cylinder heads that meet high - precision requirements. Cylinder heads produced by gravity casting perform excellently in terms of strength and sealing, being able to meet the needs of efficient engine operation.
1.3 Transmission Housings
Transmission housings need to possess certain strength and dimensional accuracy to accommodate and protect the internal gears, shafts, and other transmission components. Gravity casting can manufacture relatively large - sized and regularly shaped transmission housings, and the cost is relatively low, making it suitable for mass production. Many automotive manufacturing enterprises adopt gravity casting to produce transmission housings, effectively reducing production costs and improving production efficiency.
2. Parts in the Aerospace Field
2.1 Non - critical Structural Components
Although the aerospace field has extremely high requirements for the performance of parts, some non - critical structural components, such as parts of aircraft frames and brackets, can be produced by gravity casting. These components need to have certain strength and dimensional stability. Gravity casting can take advantage of its ability to manufacture large - sized castings to produce parts that meet the requirements. At the same time, through strict quality control, the products are ensured to meet the relevant aerospace standards. For example, an aerospace manufacturing company uses gravity casting to produce the wing frames of aircraft. While ensuring strength, it realizes lightweight design and improves the overall performance of the aircraft.
2.2 Some Engine Components
Some components of aircraft engines, such as the intake casings, can also be produced by gravity casting under the premise of meeting specific performance requirements. These components have relatively complex shapes. Gravity casting can achieve the forming of complex shapes while ensuring certain strength and accuracy, providing support for the stable operation of the engine.
3. Parts in the Machinery Manufacturing Industry
3.1 Large - scale Mechanical Parts
In machinery manufacturing, many large - scale mechanical parts, such as large - scale gears and boxes, are suitable for gravity casting. These parts are large in size, and gravity casting can achieve one - time molding, reducing processing procedures. Moreover, the cost advantage of gravity casting is particularly prominent in the production of large - sized parts. For example, a heavy - machinery manufacturing enterprise uses gravity casting to produce large - scale gears. By optimizing process parameters, the quality and production efficiency of the gears are improved.
3.2 Wear - resistant Parts
Some mechanical parts that need to possess wear - resistant properties, such as the jaw plates of crushers and the liners of ball mills, can also be produced by gravity casting. Gravity casting can make the liquid metal fully fill the mold, forming a dense structure and improving the wear resistance of the parts. At the same time, by selecting appropriate casting materials, the wear - resistant performance of the parts can be further enhanced, extending their service life.
4. Parts in the Shipbuilding Industry
4.1 Marine Propellers
Marine propellers are key components of the ship's propulsion system. They have complex shapes, large sizes, and high requirements for strength and corrosion resistance. Gravity casting can manufacture propellers that meet these requirements, and the weight of a single propeller can reach several tons. Through reasonable mold design and control of the casting process, the precise shape of the propeller blades can be ensured, improving the ship's propulsion efficiency.
4.2 Ship Engine Components
Some components of ship engines, such as the engine bodies and cylinder liners, are also suitable for gravity casting. These components need to withstand high pressure and temperature. Castings produced by gravity casting have good strength and sealing performance, being able to meet the long - term stable operation requirements of ship engines.
In conclusion, gravity casting is suitable for the production of parts in many industries that are complex in shape, large in size, or have certain cost requirements. By reasonably selecting the casting process and optimizing the production process, gravity casting can provide high - quality and low - cost parts for various industries, promoting the development of modern manufacturing.