Ductile iron pipe casting process
2025-01-21 15:56:03 hits:0
Tiegu is a casting manufacturer and supplier. The ductile iron pipes produced by Tiegu are widely used in infrastructure construction such as water supply, drainage, and gas transportation due to their high strength, high toughness, and corrosion resistance. Their excellent performance stems from a precise casting process.
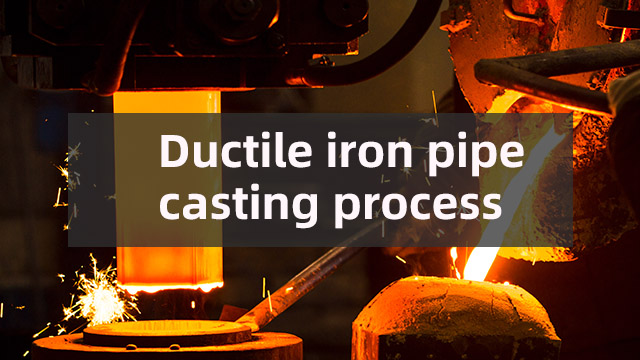
I. Raw Material Preparation
The main raw materials for ductile iron pipes include ductile cast iron, scrap steel, nodulizers, and inoculants. High - quality pig iron with low sulfur and phosphorus content is selected to ensure the purity of the molten iron. Scrap steel is used to adjust the chemical composition and carbon equivalent. Nodulizers (such as magnesium - based ones) cause the graphite to crystallize into spherical shapes, improving toughness; inoculants (such as ferrosilicon) refine the graphite spheres and improve the mechanical properties. For example, in a urban water supply project served by Tiegu, the sulfur and phosphorus content of pig iron was strictly controlled, and the proportion of scrap steel, as well as the dosage of nodulizers and inoculants, was precisely adjusted.
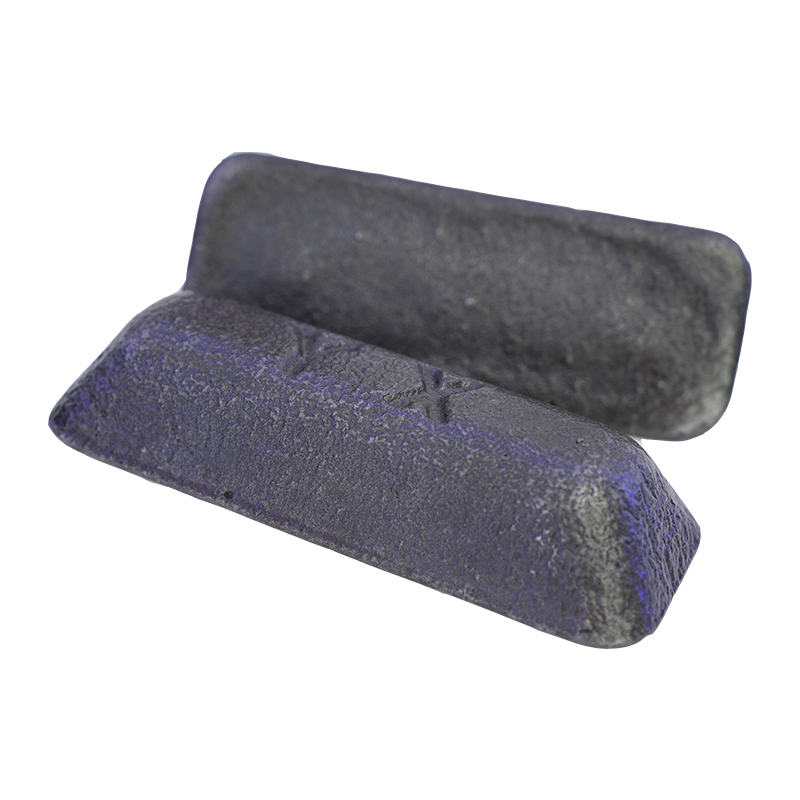
II. Melting Process
The commonly used melting process is the cupola - electric furnace duplex melting. The cupola quickly melts the raw materials, and then the electric furnace is used for refining. In the electric furnace, the temperature is controlled, and alloying elements are added to optimize the chemical composition. The electromagnetic stirring makes the composition more uniform.
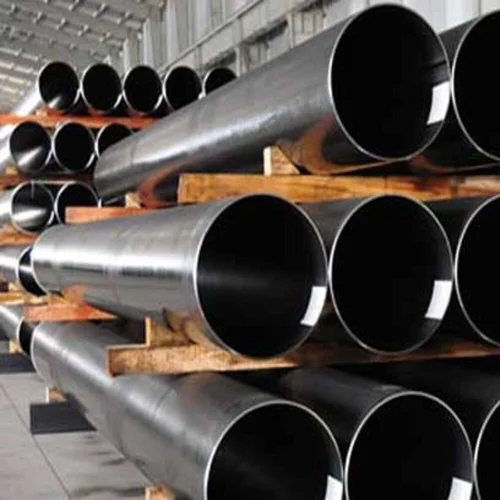
III. Nodulizing and Inoculating Treatment
After the molten iron meets the standards, nodulizing treatment is carried out. The nodulizer changes the graphite from flaky to spherical. The temperature and time during this process are strictly controlled. Subsequently, inoculating treatment is carried out, and the inoculant promotes the refinement and growth of graphite spheres. For example, when Tiegu was manufacturing a drainage pipeline, the temperature and time of nodulizing and inoculating were precisely controlled, resulting in a nodulizing rate of over 90% and improving the performance of the pipes.
IV. Casting and Molding
Centrifugal casting is mostly used. The molten iron is evenly distributed to form pipes by centrifugal force, which has high efficiency and good quality. The rotational speed of the mold, the casting temperature, and the casting speed affect the quality.
V. Heat Treatment and Post - processing
After casting, annealing is often carried out to eliminate stress and improve performance. Then, cutting, grinding, and anti - corrosion treatment are carried out. In the renovation of a coastal water supply network, after annealing treatment, the cutting was precise, the grinding was fine, and hot - dip galvanizing was used for anti - corrosion, enhancing the corrosion resistance of the pipes.
VI. Quality Inspection
Inspection is carried out throughout the whole process. The composition and properties of raw materials are inspected, the temperature and composition during melting are monitored, the graphite morphology, nodulizing rate, and mechanical properties are checked after casting, and appearance, dimension, and pressure tests are carried out on the finished products. In a municipal drainage project, each link was strictly inspected to ensure the quality of the pipes.
The casting process of ductile iron pipes is complex and sophisticated, with each link closely related. Only by strictly controlling the process can high - quality pipes be produced to meet the construction requirements. With the development of science and technology, this process will continue to be optimized and innovated.
If you have any demands or questions regarding ductile iron pipes or ductile cast iron, please feel free to contact us. We will wholeheartedly respond to every inquiry from you and provide you with high - quality services.