Foundry Environmental Requirements
2025-01-21 17:20:10 hits:0
In the modern industrial system, foundries, as a fundamental part of the industry, undertake the important task of producing various metal castings. However, traditional foundry processes often come with numerous environmental problems during production, such as exhaust gas emissions, wastewater generation, and waste residue accumulation. With the increasing awareness of environmental protection and the continuous improvement of environmental regulations, foundries are facing more stringent environmental requirements. This is not only a challenge but also an important opportunity to promote their sustainable development.
I. Exhaust Gas Emission Control
During the foundry process, a large amount of exhaust gas containing dust and harmful gases is generated. For example, in the smelting process, the melting of metals releases smoke and dust, which contains various metal oxides and harmful impurities. In the molding and core - making processes, materials such as binders produce volatile organic compounds (VOCs) when heated.
To meet environmental requirements, foundries need to install highly efficient exhaust gas treatment equipment. Bag filters and electrostatic precipitators are commonly used dust - handling devices that can effectively capture particulate matter in the exhaust gas, ensuring that the emission concentration meets national standards. For harmful gases such as sulfur dioxide and nitrogen oxides, desulfurization and denitrification technologies can be used for treatment. For VOCs, methods such as adsorption - concentration and catalytic combustion can be used to convert them into harmless substances before emission. Through these measures, foundries can significantly reduce the pollution of exhaust gas to the atmospheric environment.
To meet environmental requirements, foundries need to install highly efficient exhaust gas treatment equipment. Bag filters and electrostatic precipitators are commonly used dust - handling devices that can effectively capture particulate matter in the exhaust gas, ensuring that the emission concentration meets national standards. For harmful gases such as sulfur dioxide and nitrogen oxides, desulfurization and denitrification technologies can be used for treatment. For VOCs, methods such as adsorption - concentration and catalytic combustion can be used to convert them into harmless substances before emission. Through these measures, foundries can significantly reduce the pollution of exhaust gas to the atmospheric environment.
II. Wastewater Treatment and Reuse
The wastewater in foundry production mainly comes from casting cleaning, equipment cooling, and workshop floor flushing. This wastewater contains a large amount of suspended solids, heavy metal ions, and residues of chemical agents. If discharged directly without treatment, it will cause serious damage to the aquatic ecosystem.
Foundries should establish a complete wastewater treatment system. First, physical methods such as sedimentation and filtration are used to remove suspended solids in the wastewater. Then, chemical precipitation, ion - exchange and other technologies are adopted to remove heavy metal ions. For organic pollutants, biological treatment processes can be used for degradation. The treated up - to - standard water can be recycled to production processes with lower water quality requirements, such as the primary cleaning of castings and workshop floor flushing, thus achieving the recycling of water resources, reducing the intake of fresh water resources, and reducing the pressure on the water environment.
Foundries should establish a complete wastewater treatment system. First, physical methods such as sedimentation and filtration are used to remove suspended solids in the wastewater. Then, chemical precipitation, ion - exchange and other technologies are adopted to remove heavy metal ions. For organic pollutants, biological treatment processes can be used for degradation. The treated up - to - standard water can be recycled to production processes with lower water quality requirements, such as the primary cleaning of castings and workshop floor flushing, thus achieving the recycling of water resources, reducing the intake of fresh water resources, and reducing the pressure on the water environment.
III. Comprehensive Utilization and Disposal of Waste Residue
The waste residues generated during the foundry process mainly include smelting furnace slag and casting leftovers. If these waste residues are not properly treated, they will not only occupy a large amount of land resources but may also pollute the soil and groundwater due to the leakage of harmful substances.
Foundries should actively explore ways for the comprehensive utilization of waste residues. For example, after crushing and grinding, smelting furnace slag can be used as a raw material for building materials, such as in the production of cement and concrete aggregates. Casting leftovers can be returned to the smelting furnace for remelting to achieve the recycling of metals. For waste residues that cannot be comprehensively utilized, they need to be safely landfilled in accordance with relevant regulations or entrusted to professional institutions with qualifications for disposal, ensuring that their impact on the environment is minimized.
Foundries should actively explore ways for the comprehensive utilization of waste residues. For example, after crushing and grinding, smelting furnace slag can be used as a raw material for building materials, such as in the production of cement and concrete aggregates. Casting leftovers can be returned to the smelting furnace for remelting to achieve the recycling of metals. For waste residues that cannot be comprehensively utilized, they need to be safely landfilled in accordance with relevant regulations or entrusted to professional institutions with qualifications for disposal, ensuring that their impact on the environment is minimized.
IV. Noise Pollution Prevention and Control
The production equipment in foundries, such as smelting furnaces, fans, and crushers, generates high - intensity noise during operation, which has an adverse impact on the surrounding environment and the health of employees.
To reduce noise pollution, foundries need to take a series of noise - reduction measures. In terms of equipment selection, low - noise and environmentally friendly equipment should be preferentially selected, and the equipment should be reasonably arranged, away from residential and office areas. At the same time, noise - reduction devices such as shock absorbers and mufflers should be installed on high - noise equipment, and the workshop should be sound - proofed, for example, by decorating the walls and roof with sound - absorbing materials. Through these measures, the noise emissions of foundries can be effectively reduced, creating a good working and living environment.
To reduce noise pollution, foundries need to take a series of noise - reduction measures. In terms of equipment selection, low - noise and environmentally friendly equipment should be preferentially selected, and the equipment should be reasonably arranged, away from residential and office areas. At the same time, noise - reduction devices such as shock absorbers and mufflers should be installed on high - noise equipment, and the workshop should be sound - proofed, for example, by decorating the walls and roof with sound - absorbing materials. Through these measures, the noise emissions of foundries can be effectively reduced, creating a good working and living environment.
V. Environmental Management and Supervision
In addition to meeting environmental requirements at the technical level, foundries also need to establish a sound environmental management system. Complete environmental protection regulations should be formulated to clarify the environmental responsibilities of various departments and positions, and environmental protection work should be incorporated into the performance evaluation system to improve employees' awareness of environmental protection and sense of responsibility.
Moreover, strengthening environmental monitoring and supervision is of great importance. Foundries should regularly monitor the emissions of pollutants such as exhaust gas, wastewater, and noise to ensure that all indicators meet environmental standards. At the same time, they should actively cooperate with the supervision and inspection of environmental protection departments, take the initiative to accept the supervision of the public, and promptly discover and rectify existing environmental problems.
Moreover, strengthening environmental monitoring and supervision is of great importance. Foundries should regularly monitor the emissions of pollutants such as exhaust gas, wastewater, and noise to ensure that all indicators meet environmental standards. At the same time, they should actively cooperate with the supervision and inspection of environmental protection departments, take the initiative to accept the supervision of the public, and promptly discover and rectify existing environmental problems.
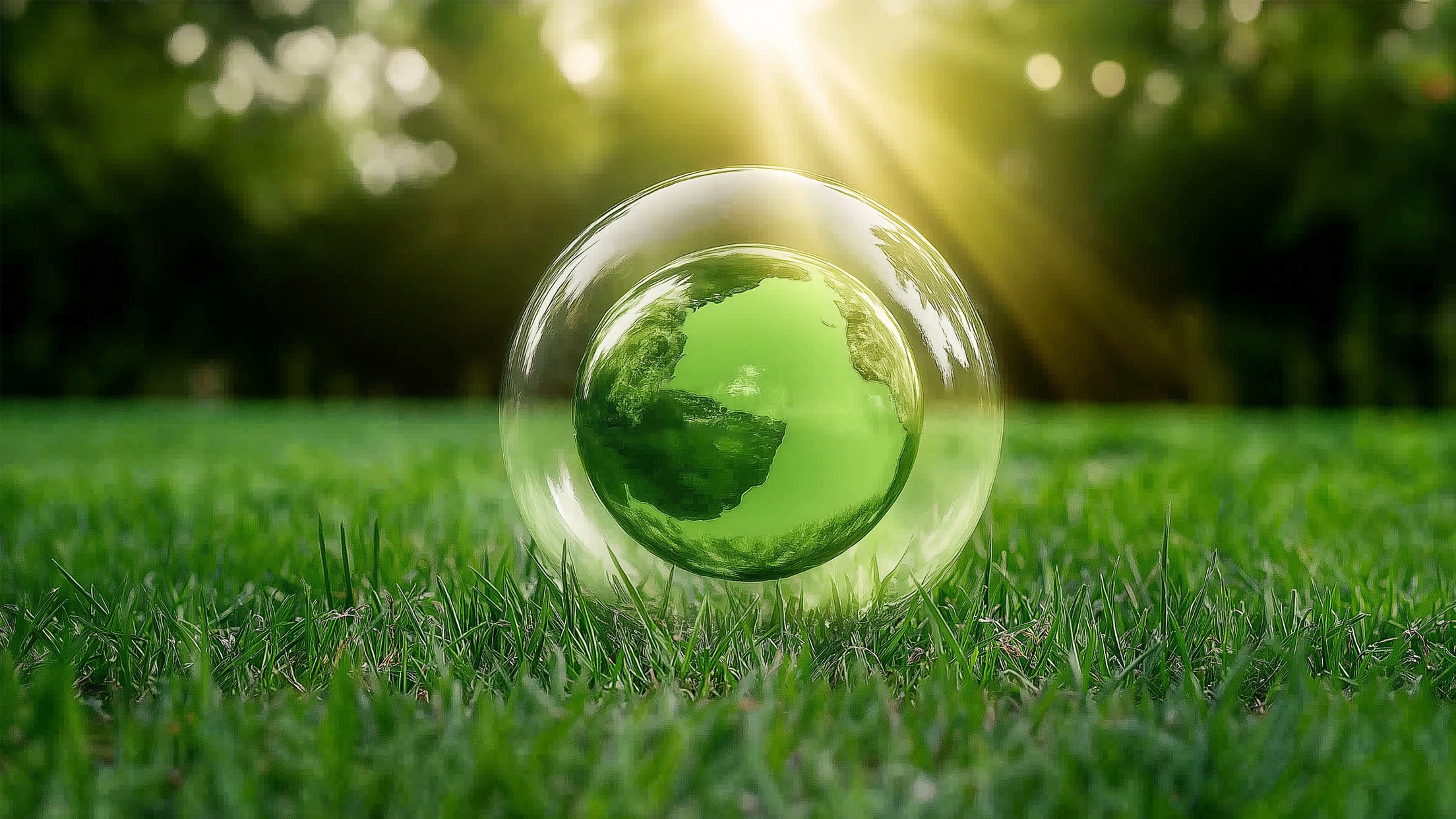
As a professional casting production and provider in the industry, Tiegu has always upheld a high sense of social responsibility and actively and resolutely responded to the national environmental protection call. With advanced production techniques, complete environmental protection facilities, and a professional technical team, Tiegu demonstrates strong foundry capabilities. While ensuring product quality, it is committed to contributing to environmental protection and setting an environmental protection benchmark for the industry. Please feel free to choose to cooperate with Tiegu.