Painting of Cast Iron Parts
2025-01-20 15:10:36 hits:0
In the field of metal casting and painting, the painting of cast iron parts holds a significant position. Due to the characteristics of cast iron itself, its painting process and applications have many unique features.
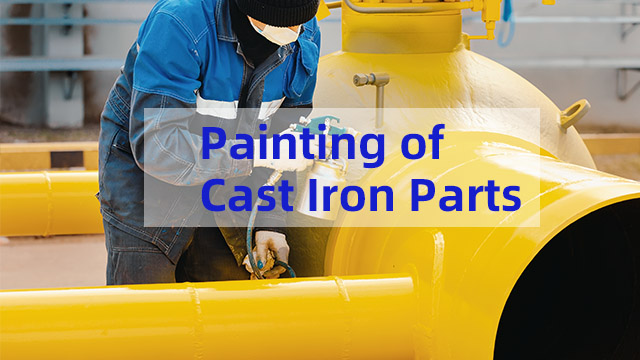
I. Key Points of the Painting Process for Cast Iron Parts
(I) Special Considerations in the Casting Stage
Cast iron has a relatively high carbon content. During high - temperature melting, the temperature curve needs to be precisely controlled to ensure the fluidity and purity of the molten iron. Compared with other metals such as cast steel, the fluidity of cast iron molten iron is slightly worse. Therefore, the design of the mold should pay extra attention to the layout of the gating system and risers to ensure that the molten iron fills the mold evenly and reduce casting defects such as gas holes and shrinkage cavities. If these defects appear on the surface of the casting, they will seriously affect the subsequent painting effect.
(II) Fine Operations in Surface Pretreatment
The surface of cast iron parts is usually relatively rough and may have problems such as sand holes and sand inclusions. During sandblasting, it is necessary to select the appropriate sand particle size and sandblasting pressure according to the surface condition of the cast iron parts and the expected roughness. Coarser sand particles can quickly remove the oxide scale and impurities, but may make the surface too rough and affect the flatness of the coating; finer sand particles can make the surface more delicate, but the cleaning efficiency may be lower. Degreasing treatment is crucial for cast iron parts because a large amount of release agent is often used during the casting process for easy demolding. If the release agent remains, it will greatly reduce the adhesion of the coating. During pickling or phosphating treatment, the concentration of the solution and the treatment time should be strictly controlled to prevent excessive corrosion of the cast iron parts.
(III) Targeted Selection in Painting Operations
For cast iron parts, due to their relatively high surface roughness, electrostatic spraying can better utilize the principle of electrostatic adsorption to make the paint adhere to the surface more evenly. However, before electrostatic spraying, it is necessary to ensure that the surface of the cast iron parts has good electrical conductivity to avoid uneven local charge distribution affecting the coating quality. Powder spraying is also a commonly used method, especially suitable for cases where high requirements are placed on the thickness and hardness of the coating. After powder is cured by high - temperature baking, it can form a firm and wear - resistant coating. When selecting the paint, the use environment of the cast iron parts should be considered. If it is used in a humid environment, a paint with good rust - prevention performance should be selected; if it is used outdoors, the weather resistance of the paint also needs to be considered.
(IV) Strict Control in Drying and Curing
The drying and curing process has a great impact on the painting quality of cast iron parts. When drying solvent - based paints, the temperature and ventilation conditions should be well - controlled. Excessive temperature may cause the surface of the coating to dry too quickly, forming defects such as pinholes; poor ventilation will slow down the evaporation of the solvent, affecting the drying speed and coating performance. For the baking and curing of powder coatings, it is necessary to strictly follow the process parameters provided by the paint supplier. Deviations in temperature and time may lead to incomplete or over - curing of the coating, reducing the protective performance and aesthetics of the coating.
II. Notable Advantages of Painting Cast Iron Parts
(I) Excellent Protective Performance
Cast iron is prone to rust and corrosion in humid, acidic and alkaline environments. Painting can form a dense protective film on its surface, effectively blocking the erosion of oxygen, moisture and corrosive chemical substances. For example, painting on the cast iron pipes and equipment in sewage treatment plants can greatly extend their service life and reduce the maintenance and replacement costs caused by corrosion. In addition, for cast iron mechanical parts used in industrial atmospheric environments, painting can prevent surface oxidation and wear, ensuring the normal operation of the equipment.
(II) Good Decoration Effect
By selecting paints with different colors, gloss levels and textures, a variety of appearance effects can be created for cast iron parts. In furniture manufacturing, after being painted, cast iron parts can present various styles, such as the deep brown of the retro style and the white of the simple modern style, meeting the aesthetic needs of different consumers. In the field of architectural decoration, cast iron railings, flower windows, etc., after being carefully painted, can be integrated with the overall architectural style, enhancing the aesthetics and artistic value of the building.
(III) Increasing Product Added Value
Cast iron parts that have been carefully painted are significantly improved in appearance and performance, thus increasing the added value of the product. In the handicraft market, exquisite cast iron sculptures, after a delicate painting process, are vivid in color and texture, and their prices are often several times that of unpainted castings. In the machinery manufacturing industry, high - quality painting makes cast iron parts not only reliable in quality but also exquisite in appearance, enhancing the competitiveness of products in the market.
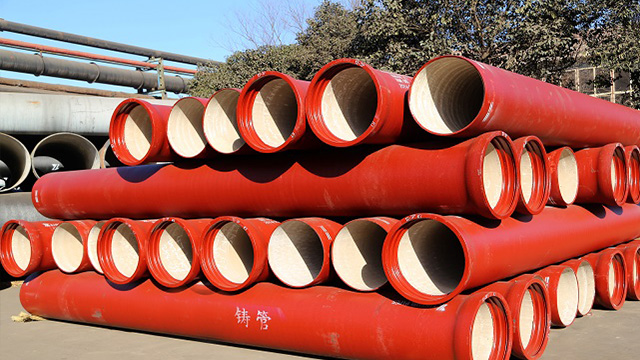
III. Wide Application Fields of Painting Cast Iron Parts
(I) Construction Field
Cast iron is widely used in the construction field, such as load - bearing components in building structures, stair handrails, door and window accessories, etc. After these cast iron parts are painted, they can not only enhance their corrosion resistance and adapt to different climate conditions but also play a decorative role. In European - style buildings, cast iron floral ornaments, after being painted gold or bronze, create a magnificent and elegant atmosphere; in modern minimalist - style buildings, black or white painted cast iron components show a simple and elegant style.
(II) Machinery Manufacturing
Cast iron parts are widely used in various mechanical equipment, such as machine tool beds, engine blocks, gearbox housings, etc. Painting plays a protective and marking role for these cast iron parts. After the machine tool bed is painted, it can prevent corrosion by coolant, cutting fluid, etc. At the same time, different colors of paint can be used to distinguish different functional areas or operation instructions. Painting the engine block can prevent the erosion of the block by internal lubricating oil and extend its service life.
(III) Household Items
Household items made of cast iron, such as tables, chairs, lamps, ornaments, etc., are both beautiful and durable after being painted. Painted cast iron tables and chairs can become the highlights in the home space, adding personality and artistic sense to the indoor environment. After being painted, cast iron lamps can not only prevent rust but also create a unique lighting atmosphere through different colors and gloss levels.
(IV) Garden Landscape
In garden landscapes, cast iron parts are often used to make sculptures, railings, flower racks, etc. Painting can make these cast iron parts better integrate into the natural environment and resist the erosion of the outdoor environment. For example, green - painted cast iron railings echo with the surrounding green plants, creating a harmonious landscape effect; bronze - painted cast iron sculptures add a historical and cultural atmosphere to the garden.
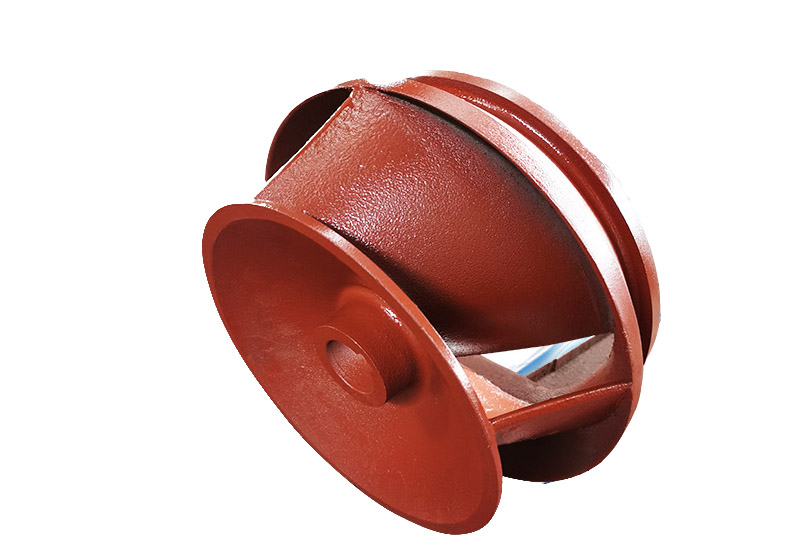
IV. Challenges and Countermeasures in Painting Cast Iron Parts
(I) Coating Adhesion Problems
Due to the possible presence of oil stains, impurities and loose oxide layers on the surface of cast iron parts, the adhesion of the coating is insufficient, and peeling is likely to occur. The countermeasure is to strengthen the surface pretreatment process, use appropriate degreasing agents to thoroughly remove oil stains, remove the oxide layer by sandblasting and other methods, and ensure that the surface roughness is appropriate. In addition, selecting a primer that is compatible with the cast iron material can effectively improve the coating adhesion.
(II) Coating Defects Caused by Gas Holes and Sand Holes
There may be gas holes and sand holes in cast iron parts themselves. After painting, problems such as pinholes and blisters are likely to occur at these defect locations. To solve this problem, efforts should be made to minimize the generation of gas holes and sand holes during the casting process, which can be achieved by optimizing the casting process and controlling the quality of the molten iron. For existing gas holes and sand holes, pretreatment methods such as filling and grinding can be used before painting to ensure a flat surface.
(III) Pressure Brought by Environmental Protection Requirements
In traditional painting processes, solvent - based paints contain a large amount of volatile organic compounds (VOCs), which pollute the environment. To meet environmental protection requirements, the use of environmentally friendly paints such as water - based paints and powder paints should be promoted. At the same time, improve painting equipment and processes, increase paint utilization, and reduce exhaust gas emissions. For example, the use of high - efficiency electrostatic spraying equipment and closed - type painting booths, combined with exhaust gas purification treatment devices, can effectively reduce VOCs emissions.
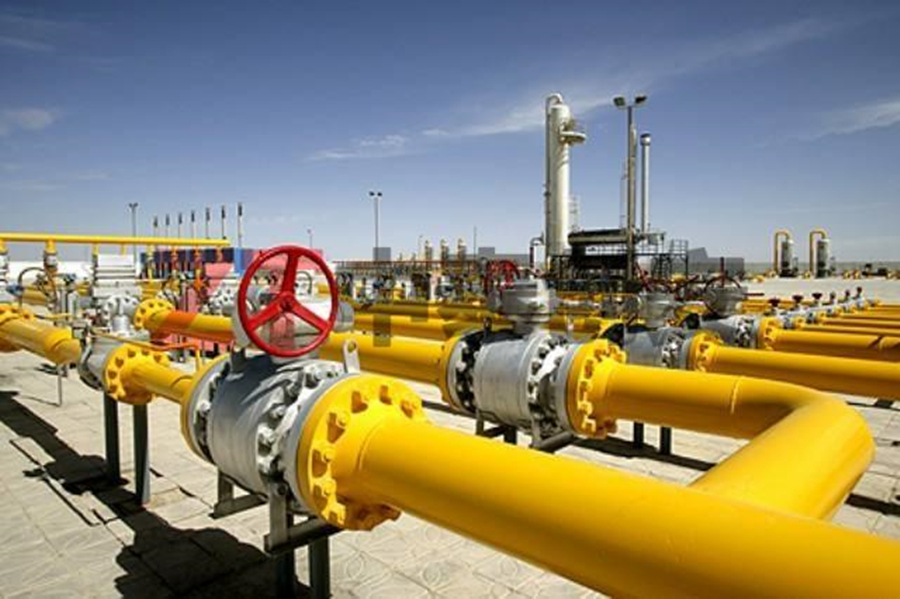
V. Future Development Trends of Painting Cast Iron Parts
(I) Application of Intelligent Painting Technology
With the development of technology, intelligent painting equipment will gradually be applied to the field of painting cast iron parts. These devices can use sensors to monitor parameters such as the surface condition of cast iron parts and the thickness of the paint in real - time, and automatically adjust the painting process parameters according to preset programs to achieve precise painting. This can not only improve the painting efficiency and quality stability but also reduce errors caused by manual operations.
(II) R & D and Application of New Paints
In the future, new paints with special functions will continue to emerge and be applied to the painting of cast iron parts. For example, self - healing paints can automatically repair when the coating is slightly damaged, maintaining the protective performance; nano - paints have excellent corrosion resistance, wear resistance and antibacterial properties. These new paints will further enhance the performance and service life of cast iron parts.
(III) Continuous Development of Green and Environmentally Friendly Processes
Against the background of increasing environmental awareness, green and environmentally friendly painting processes for cast iron parts will become the mainstream. In addition to continuing to promote environmentally friendly paints, more environmentally friendly surface pretreatment methods and exhaust gas treatment technologies will also be explored. For example, new surface pretreatment technologies such as plasma treatment can be used to replace traditional chemical treatment methods to reduce wastewater discharge; more efficient exhaust gas purification technologies can be developed to achieve zero or low - emission of VOCs.
As an important process, the painting of cast iron parts plays a key role in various fields. By continuously optimizing the process, addressing challenges, and keeping up with technological development trends, the painting of cast iron parts will bring us more high - quality, beautiful and environmentally friendly cast iron products, promoting the sustainable development of related industries.
Previous: Cast Iron and Cast Steel