Cast Iron and Cast Steel
2025-01-20 14:36:31 hits:0
In modern manufacturing, casting, with its ability to produce durable and high-quality components, has become one of the most favored processes. It can not only achieve highly detailed presentations but also eliminates the need for complex additional manufacturing or assembly processes. Moreover, it is suitable for the forming of various materials. Among them, cast iron and cast steel, as two of the most popular casting materials, shine brightly in a wide range of application fields with their excellent mechanical properties.
Tiegu, a leading casting manufacturer in China, focuses on using cast iron and cast steel as the main raw materials to create various high-quality castings.
Cast iron encompasses gray cast iron, ductile cast iron, and malleable cast iron, with a carbon content exceeding 2%. Cast steel, on the other hand, includes plain carbon steel and alloy steel, with a carbon content lower than 2%. Although the differences between the two in chemical composition and raw materials are subtle, there are significant disparities in physical properties, performance, and many other aspects.
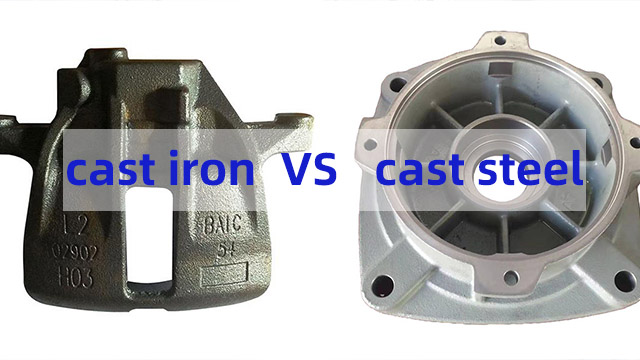
I. Performance Analysis
(I) Characteristics of Cast Iron
Gray Cast Iron: It possesses excellent casting properties, remarkable vibration damping, good wear resistance, excellent machinability, and low notch sensitivity. However, its tensile strength and elongation are relatively low, making it more suitable for manufacturing metal parts with low mechanical requirements, such as protective covers, lids, oil pans, etc. Nevertheless, high-grade gray cast iron castings can withstand relatively large loads and have certain sealing and corrosion resistance properties, and are often used in medium-pressure valves, cylinders, and other components.
Ductile Cast Iron and Malleable Cast Iron: Compared with gray cast iron, they have higher strength, better ductility, heat resistance, and more excellent toughness. Therefore, their application range is more extensive, and in some scenarios, ductile cast iron can even replace carbon steel. However, the production technology of ductile cast iron requires high precision, and the process is complex, resulting in more casting defects and relatively high production costs. Even so, in fields such as pressure pipelines and fittings, automotive manufacturing, agriculture, and construction, ductile cast iron still occupies a place with its advantages.
(II) Characteristics of Cast Steel
Design Advantages: The greatest advantage of cast steel lies in its high design flexibility. Casting designers have great freedom in design, especially suitable for the manufacturing of parts with complex shapes and hollow cross-sections.
Performance Advantages: It has flexibility in metallurgical manufacturing and strong variability. Different chemical compositions can be flexibly selected and precisely controlled according to different project requirements. Through various heat treatment methods, mechanical properties and performance can be adjusted within a large range. In addition, cast steel also has good weldability and machinability and can be widely applied to various working conditions. Its mechanical properties surpass most other casting alloys and are excellent in the manufacturing of components subject to high tensile stress or dynamic loads. For key large components such as low-temperature or high-temperature pressure vessel castings, cast steel is the top choice.
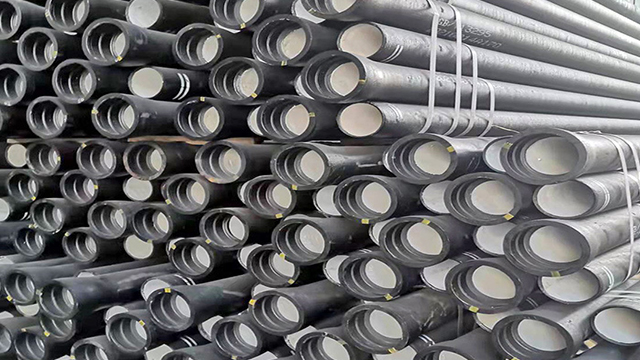
II. Comparative Analysis of Differences
(I) Differences in Material Properties
Cast iron is mainly composed of iron, carbon, and silicon, with a carbon content usually exceeding 2.11% and is a type of iron-carbon alloy. The carbon in cast iron mostly exists in the form of graphite and sometimes in the form of cementite. Cast iron also contains 1% - 3% silicon, as well as elements such as manganese, phosphorus, and sulfur. Some special cast irons also contain elements such as nickel, chromium, molybdenum, aluminum, copper, boron, and vanadium.
Cast steel has iron and carbon as its main elements, with a carbon content between 0.15% - 0.60%. Cast steel can be divided into cast carbon steel and cast alloy steel. Among them, the strength and hardness of cast carbon steel increase with the increase in carbon content. Cast alloy steel can be further divided into low-alloy cast steel (total alloy element content ≤ 5%), medium-alloy cast steel (5% - 10%), and high-alloy cast steel (≥ 10%) according to the total amount of alloy elements.
Castability: Cast iron performs excellently in casting and is relatively easy to operate.
Machinability: Cast iron is generally easier to machine than cast steel. The graphite structure in cast iron makes it easier and more uniform to shed during the machining process, while steel is difficult to maintain a consistent consistency during cutting, which is likely to cause tool wear and increase production costs.
Vibration Damping: The vibration damping performance of cast iron is outstanding. The graphite structure in gray cast iron, especially the flake structure, is extremely beneficial for absorbing vibrations.
Compressive Strength: Generally, the compressive strength of cast iron is better than that of cast steel.
Impact Resistance: Cast steel performs excellently in impact resistance. It can withstand sudden impacts well and is not easy to bend, deform, or break, thanks to its excellent toughness.
Corrosion Resistance: Cast iron has a certain degree of corrosion resistance, while the stainless steel alloy in cast steel has more excellent corrosion resistance.
Wear Resistance: Under friction and wear conditions, cast iron usually has better resistance to mechanical wear than steel. The high graphite content in cast iron can produce a graphite dry lubricant, reducing surface wear. However, the wear resistance of cast steel can also be effectively improved by adding alloys.
(II) Differences in Other Characteristics
Melting Point and Pouring Ability: The melting temperature of iron is approximately 2300°F, and that of steel is 2600°F. Both need to be poured into the mold at a relatively high temperature. The pouring ability of cast iron is stronger because it has good fluidity and can be smoothly poured at a lower temperature, and its shrinkage rate is relatively small. This makes it an ideal choice for building structures or ornate iron products, such as fences and street facilities.
Cost: Overall, the cost of cast iron is usually lower than that of cast steel. This is mainly because the production process of cast iron is relatively simple, and the raw material cost is lower. Cast steel has various prefabricated forms, such as plates, bars, etc., which can be machined or assembled according to specific applications. In some cases, manufacturing using existing steel products may be more cost-effective.
III. Material Selection Suggestions
(I) Scenarios for Selecting Cast Iron
- When the mechanical property requirements are not high, gray cast iron (with the lowest price) is the first choice. For example, in the manufacturing of some daily necessities or simple mechanical parts with low strength requirements, gray cast iron can meet the needs while reducing costs.
- If good heat insulation performance is required, cast iron is the first choice. Cast iron has a relatively high heat capacity. In some equipment or components that need to maintain stable temperature, such as the lining of some industrial furnaces and heat insulation containers, the heat insulation characteristics of cast iron can play an important role.
- For applications with high requirements for compressive strength, cast iron is a better choice. For example, in building foundations, large mechanical bases, and other structures that need to bear huge pressure, cast iron can provide reliable support with its excellent compressive performance.
- If you need an economical product, please choose cast iron because the production cost of gray cast iron is lower.
- When the demand is extremely large, such as tens of thousands of pieces per year, cast iron products made by automatic molding or shell molding processes are good choices.
- Generally, cast iron is suitable for low-temperature and low-pressure application scenarios. In some pipeline systems and simple storage containers operating under normal temperature and pressure, cast iron can operate stably and at a relatively low cost.
(II) Scenarios for Selecting Cast Steel
- If you pursue perfect surface quality and precise dimensional control, you can consider cast steel parts produced by the silica sol investment casting process, although their price is relatively high. For example, in the manufacturing of some precision instrument parts and high-end mechanical parts with extremely high requirements for appearance and dimensional accuracy, cast steel parts produced by this process can meet strict quality standards.
- When the material needs to have good ductility and strength, please choose cast steel. For example, in fields such as aerospace and automotive manufacturing, where strict requirements are placed on material performance, the high strength and good ductility of cast steel can ensure the reliability and safety of components under complex stress conditions.
- If the final product needs to be used under impact load conditions, please choose cast steel. Cast steel can meet the requirements due to its high toughness. In components of mining machinery and construction equipment that often bear impacts, the impact resistance of cast steel can ensure the long-term stable operation of the equipment and reduce failure and maintenance costs.
- For applications that require good thermal and electrical conductivity, please choose cast steel. In some electrical equipment components, heat exchangers, and other products that require thermal and electrical conductivity, cast steel can exert its excellent physical properties to ensure the efficient operation of the equipment.
- In high-temperature and high-pressure application scenarios, cast steel is the first choice. For example, in high-temperature and high-pressure pipelines, pressure vessels, and other key equipment in the petrochemical and power industries, cast steel can withstand extreme working conditions and ensure the safety and stability of the production process.
Through the above comprehensive analysis of cast iron and cast steel, I believe you can clearly understand the differences and respective advantages of the two. Cast iron is widely used in industrial production due to its low cost and good casting performance; while cast steel, with its high strength, high temperature resistance, and weldability, has become the preferred material for manufacturing high-strength parts.
As a professional casting factory for cast iron, cast carbon steel, and cast steel, Tiegu sincerely looks forward to your letter or consultation. If you have any casting needs, please feel free to contact us at any time. We will wholeheartedly serve you and help your project achieve complete success.
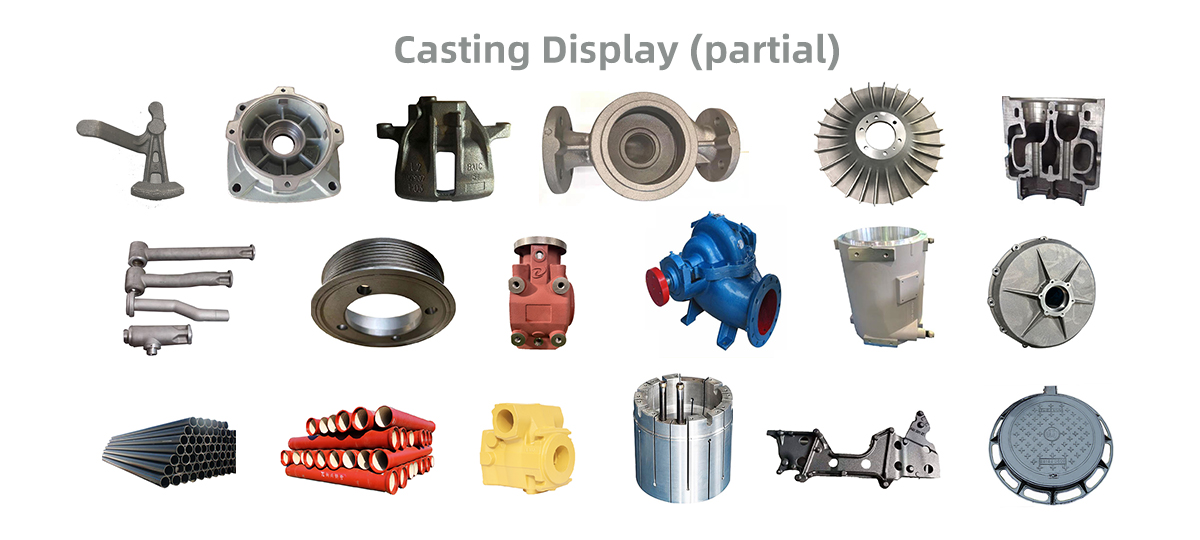