Blast Furnace and Pig Iron: Relationship
2025-01-17 17:10:17 hits:0
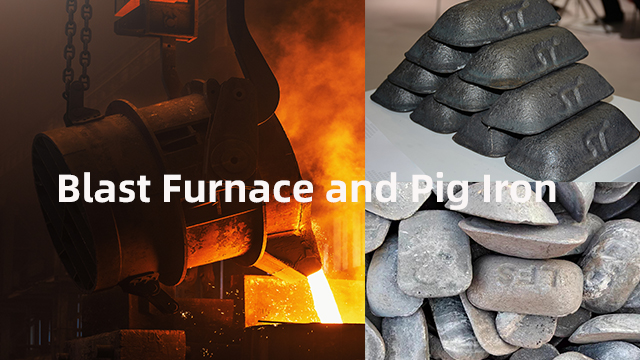
A blast furnace is a shaft furnace that converts raw materials such as iron ore, coke, and flux into pig iron through a series of complex physical and chemical reactions. For every 1 ton of molten iron (i.e., the liquid form of pig iron) produced, approximately 1.6 - 1.8 tons of iron ore, 0.4 - 0.6 tons of coke, and 0.2 - 0.3 tons of flux are consumed. The production efficiency and scale of the blast furnace determine the output of pig iron. Modern large-scale blast furnaces can reach a height of over 100 meters, with a volume usually ranging from 4,000 to 5,000 cubic meters, or even larger. For example, Baosteel's No. 4 blast furnace has an effective volume of 5,800 cubic meters and can produce about 10,000 tons of pig iron per day.
The working principle of a blast furnace is based on a series of complex physical and chemical reactions. First, hot air at a high temperature of 1000 - 1300°C is blown in from the tuyeres at the lower part of the blast furnace, causing the coke to burn vigorously, with the reaction , releasing a large amount of heat, and the temperature inside the furnace can reach 1500 - 1600°C. The generated carbon dioxide reacts with coke at high temperature to form carbon monoxide: . As the main reducing agent, carbon monoxide reacts with iron oxide in the iron ore to reduce it, such as , thus reducing iron from the ore.
During this process, in order to remove impurities such as gangue in the iron ore, fluxes such as limestone need to be added. Taking limestone as an example, at high temperature, it first decomposes into calcium oxide and carbon dioxide: , and then calcium oxide reacts with acidic oxides such as silicon dioxide in the gangue to form slag, such as . As the reaction continues, the molten iron and slag gradually flow downward under the action of gravity due to their different densities and are finally separated in the hearth. The molten iron, with a higher density, sinks to the bottom of the hearth and is regularly tapped from the iron notch and sent to the steelmaking workshop; the slag floats above the molten iron and is discharged from the slag notch. Generally speaking, for every 1 ton of molten iron produced, approximately 1.6 - 1.8 tons of iron ore, 0.4 - 0.6 tons of coke, and 0.2 - 0.3 tons of flux are consumed.
In the iron - making process, the blast furnace reduces iron ore to pig iron (also known as molten iron), and pig iron is the main raw material used in the steel - making process. The blast furnace plays an indispensable role in steel production. According to statistics, more than 90% of the world's pig iron is smelted through blast furnaces. The high - efficiency and large - scale production capacity of blast - furnace iron - making provide a continuous supply of steel materials for many industries such as construction, machinery manufacturing, and the automotive industry. For example, in the construction industry, the construction of a large number of high - rise buildings, bridges, and other infrastructure every year is inseparable from the large amount of high - quality pig iron provided by blast - furnace iron - making. In the machinery manufacturing field, from large - scale mechanical equipment to precision instruments, pig iron, as a basic material, supports the development of the entire industry.
With its strong production capacity, the blast furnace provides a solid material foundation for the development of modern society and will continue to play a core role in the steel industry in the future.
As a world - leading supplier of pig - iron products, Tiegut focuses on providing high - quality pig - iron products to the international market, including but not limited to foundry pig iron, nodular pig iron, high - purity pig iron, steel - making pig iron, blast - furnace pig iron, etc. We have also established long - term and stable cooperative relationships with several large - scale pig - iron production enterprises to ensure that all products meet international quality standards and cover a variety of specifications to meet the diverse needs of global customers. For customers with large - scale projects or special needs, we provide customized services to ensure that their unique requirements are met.