Crankshaft Iron Mold Coated Sand Casting and Its Production Process Control
2025-01-14 14:24:51 hits:0
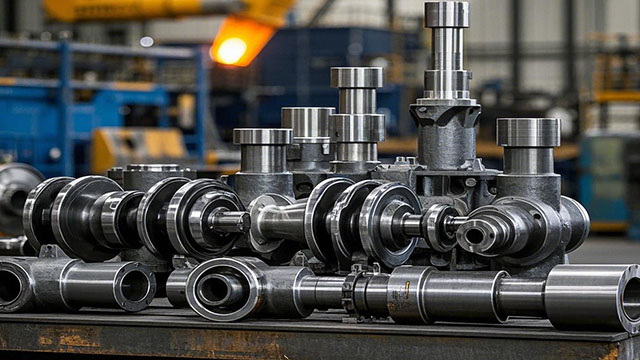
Adopting the crankshaft coated sand process for crankshaft casting not only simplifies the clay sand process, improves the material performance, but also reduces the process cost. The crankshaft coated sand process has become a development trend in the domestic shaft industry and is worthy of promotion within the industry. The crankshaft is one of the key components of the engine, and its performance directly affects the service performance and lifespan of the engine. When the crankshaft is working, it bears alternating large - load bending moments, torques, and impacts. The common failure forms are bending fatigue fracture and journal wear. Therefore, the crankshaft material is required to have high rigidity, fatigue strength, and good wear - resistance. Especially in recent years, with the increasing application of turbocharged engines, higher and higher requirements have been put forward for the internal quality, blank accuracy, and surface roughness of the crankshaft. Iron mold coated sand casting is a casting process in which a 5 - 8mm thick layer of thermosetting molding sand is evenly coated on the inner cavity of the shaped iron mold (as shown in Figure 1) to form a mold (as shown in Figure 2). Due to the good stiffness of the iron mold coated sand mold and the relatively thin coated sand layer, the casting has a fast cooling rate, fine sand particle size (generally 200 mesh). Therefore, it can significantly improve the dimensional accuracy, compactness, surface quality, grain refinement degree, and spheroidization rate of the casting, and at the same time, riser - less casting can be realized.
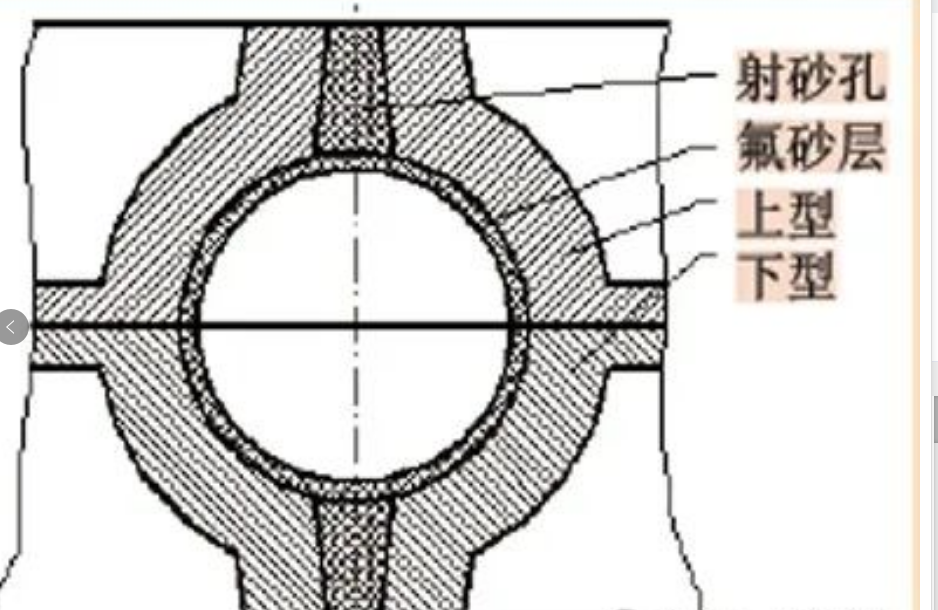
Production Process of the Iron Mold Coated Sand Line
The production process flow of the iron mold coated sand line is shown in Figure 3. Currently, there are various forms of process layout for the iron mold coated sand line, and the open - type line layout is the most common. Because it can meet the requirements of different cooling times for the production of multiple crankshaft varieties, and at the same time, it can conveniently realize the mechanization and automatic control of the movement and propulsion of the iron mold during the production process.
1. Coated Sand Molding
The coated sand molding process is a key process in iron mold coated sand casting, which directly affects the entire production process and the yield of crankshafts. Initially, the iron mold coated sand process borrowed the hot - box core shooter, with a low degree of mechanization. Now, many domestic foundry machinery manufacturers produce special iron mold coated sand equipment, and some can realize the full - process PLC touch - screen automatic control from mold closing to the removal of the iron mold after sand shooting.
(1) Iron Mold Temperature
During normal production, the iron mold temperature is generally controlled at around 230°C. If the temperature is too low, the coated sand cannot be completely cured, resulting in low shell strength and high gas evolution. If the temperature is too high, the mold shell will be burned and become brittle, or the coated sand will be cured during the flowing process, damaging the mold shell strength and easily causing sand adhesion and sand inclusion of the crankshaft. There are generally two methods for heating the iron mold for the first use. One is to put a batch of iron molds into the core kiln for heating, and then carry out molding one by one. The other is to close the cold iron molds one by one and then heat the iron molds through the pattern and the template (the template is equipped with electric heating pipes) for molding. This method is relatively slow when the new iron mold is used for the first production. During normal production, the residual heat of the iron mold can be used for coated sand, and no separate heating is required.
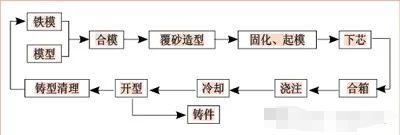
(2) Sand Shooting
Sand shooting is a process in which fluidized coated sand is blown into the cavity by low - pressure compressed air (0.4MPa), and the sand shooting time is only 1 - 2s. There are two key links in this process: one is exhaust, and the other is sand leakage. During the sand shooting process, while the coated sand is injected, the compressed air also enters the cavity. If the exhaust of the iron mold is not smooth, it will inevitably cause defects such as insufficient shooting and air pockets. The commonly used solutions are as follows: ① For the residual gas near the parting surface, four bosses 0.1 - 0.2mm higher than the template are made on the template, so that a gap is formed between the template and the iron mold to discharge the residual gas. ② Exhaust plugs are added at individual dead - end parts or exhaust grooves are engraved on the template to discharge the residual gas. These two methods are quite effective in actual production. During sand shooting, the sand shooting holes on the sand shooting head are aligned with the sand shooting holes of the iron mold, and the lower plane of the sand shooting plate is pressed tightly against the upper plane of the iron mold and then sand shooting is carried out. However, in actual production, due to the stress deformation after the iron mold is cast and processed, the deformation caused by continuous heating and cooling of the iron mold, and the bumps on the upper surface of the iron mold, a gap will be generated between the upper surface of the iron mold and the lower plane of the sand shooting plate during sand shooting, and the sand will run out from the gap during sand shooting. Sand leakage not only wastes sand, deteriorates the working environment, and causes the cavity to be not filled solidly, resulting in waste products, but also because the sand flow rate is too fast, it is very likely to cause personal injury to the operator. The commonly used methods now are: ① A silica gel pad 5mm higher than the plane is inlaid on the lower surface of the sand shooting plate. ② The sand shooting nozzle of the sand shooting plate is made into a movable and compressible type, and a compression spring is installed on the back. In this way, the sand shooting nozzle can be in close contact with the periphery of the sand shooting hole of the iron mold to avoid sand leakage. When the iron mold is severely deformed, not only the upper surface of the iron mold leaks sand, but also a large gap is generated between the lower surface of the iron mold and the mold plate, and at this time, only the upper and lower surfaces of the iron mold can be planed and then used.
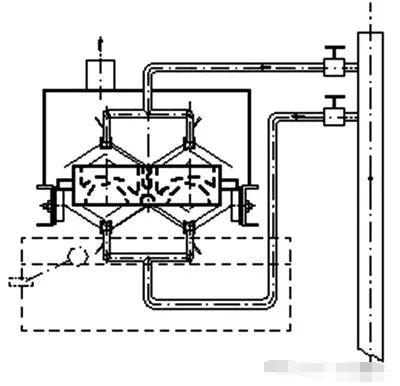
2. Iron Mold Cooling
In actual production, in order to ensure production efficiency, it is impossible to open the box when the crankshaft is cooled to about 230°C (generally, the box is opened 15 - 20 minutes after pouring). Due to the very thin coated sand layer, the temperature of the iron mold rises sharply after pouring. The temperature of the iron mold after one cycle is about 350 - 400°C, and it will get higher and higher, making normal production impossible. Because natural cooling is too slow, if water is poured on the iron mold to accelerate the cooling speed of the iron mold, it is very easy to cause the iron mold to crack. At present, domestic manufacturers producing iron mold coated sand lines do not produce special equipment for iron mold cooling. To solve the problem of iron mold cooling, we have specially designed a cooling device according to the actual situation, as shown in Figure 4 and Figure 5. The nozzle structure is shown in Figure 5. After the compressed air enters the pipe, the flow velocity of the air is accelerated through the reducing sleeve, and a larger negative pressure is formed at the copper pipe opening. The other end of the copper pipe is connected to a water tank with an oxygen tube and placed in the water in the water tank, and then water in the copper pipe is sucked out. The high - speed air flow atomizes the water, and through the cone at the pipe opening and the cone below, the mist is sprayed onto the surface of the iron mold in a conical shape. This cooling device adopts multi - head atomized cooling, so that the iron mold is cooled evenly, reducing the deformation and cracking of the iron mold and improving the service life of the iron mold. At the same time, when the water mist is sprayed onto the surface of the iron mold, a layer of high - temperature water vapor film is quickly formed on the surface of the iron mold. The high - speed air flow of the compressed air blows away the high - temperature water vapor film in time, accelerating the cooling speed of the iron mold and meeting the needs of continuous production of the production line.

3. Mold Closing
Since phenolic resin is used as a curing agent for the coated sand, a large amount of gas will be generated when the molten iron is poured into the cavity. If the gas cannot be discharged in time, it will inevitably cause casting pores and insufficient pouring defects. Therefore, in addition to designing exhaust holes on the upper - mold pattern and exhausting the coated sand about 5mm away from the upper - mold surface through the sand shooting needle, 0.5mm thick iron sheets are padded at the four corners of the parting surface during mold closing, so that a gap is formed at the parting surface to discharge the gas.
Melting, Spheroidization, Inoculation, and Pouring of Molten Iron
The iron mold coated sand process provides favorable conditions for obtaining castings with finer grains, higher spheroidization levels, better surface quality, and better mechanical properties due to the fast cooling of the casting. However, it also puts forward higher requirements for the melting, spheroidization, inoculation, and pouring of the molten iron.
1. Melting
Because the casting cooling rate is fast in the iron mold coated sand process, the inclusions and gases in the molten iron entering the cavity are not easy to float out and are very likely to form slag inclusions and pores, and at the same time, it is also easy to form cold shuts. Therefore, the production of the iron mold coated sand process requires high - temperature and clean molten iron. Now, due to the increase in the price of coke, the melting cost of the medium - frequency induction furnace is no longer higher than that of the cupola. At the same time, the medium - frequency induction furnace can obtain molten iron with stable chemical composition, high - temperature and cleanliness, and can meet the needs of continuous production. Therefore, the medium - frequency induction furnace is the best choice for melting in the iron mold coated sand process for casting crankshafts. Generally, the tapping temperature of the medium - frequency induction furnace is about 1500°C. Also, because the casting cooling rate is fast in the iron mold coated sand process and the supercooling degree of the molten iron melted by the medium - frequency induction furnace is large, the casting has a large tendency to form white cast iron, and free cementite is likely to be formed after the casting is cooled. Therefore, the carbon - silicon equivalent in the batching should be higher than that in the clay sand molding process. The commonly used chemical composition is shown in the table.
2. Spheroidization Treatment
Spheroidization treatment is an important part of the production of ductile iron crankshafts. The morphology of graphite directly affects the strength performance of the crankshaft body. Currently, the main spheroidizing agent used in China is rare - earth magnesium - silicon - iron composite spheroidizing agent. The selection of the spheroidizing agent grade mainly considers the absorption rate and whether the reaction is stable. Because the iron mold coated sand process requires a relatively high tapping temperature of the electric furnace molten iron, a lower - grade spheroidizing agent such as FeSiMg6Re1.6 is suitable. In order to reduce the secondary slag formed by the reaction of sulfur and magnesium, the residual rare - earth magnesium should not be too high. Since the current plunge - method spheroidization will generate a large amount of smoke and dust, the wire - feeding method with low - magnesium cored wire is now adopted, and the effect is more stable than the plunge - method.
3. Inoculation Treatment and Pouring
Due to the fast cooling of the iron mold coated sand process and the large supercooling degree of the electric furnace molten iron, the casting has a large tendency to form white cast iron during the solidification process. Therefore, the molten iron must be fully inoculated. Generally, two - stage inoculation treatment is carried out: the first time, 0.2% - 0.3% of silicon - barium inoculation wire is put into the ladle during the spheroidization treatment; the second time, 0.1% of in - stream inoculation is adopted during pouring, and a composite high - efficiency inoculant containing sulfur and oxygen is used, which can effectively increase the graphite nuclei, refine the grains, and delay the inoculation fading time. The particle size of the inoculant is generally 0.2 - 0.8mm, and it should not be stored for a long time to avoid moisture and oxidation. The pouring temperature is generally about 1420°C, and slag - blocking should be noted during pouring. Because the molten iron solidifies quickly and the inclusions are difficult to float up, filter plates are generally placed in the gating system.
Crankshaft Residual Heat Normalizing with Alloying
The rapid solidification of the casting and the high - temperature and pure molten iron of the medium - frequency electric furnace provide favorable conditions for the refinement of the casting grains and the improvement of the spheroidization level. Under normal production conditions, the pearlite content is generally 65% - 75%, the tensile strength is 680 - 750N/mm², and the elongation is 4% - 6%. During the molten iron treatment process, 0.5% - 6% of Cu and a small amount of trace elements Sb that strongly promote pearlitization are added. The continuous mechanization or automatic control of the iron mold coated sand line makes it easier to control the box - opening operation. When the casting temperature is about 860 - 900°C, the box is opened, and then the casting is quickly transferred to the cooling chamber for spray cooling. In this way, a ductile iron crankshaft blank with a pearlite content of 85% - 90% and mechanical properties of QT800 - 3 can be obtained. It can not only improve the high - temperature environment of the cleaning workshop, reduce round - trip transportation and primary cleaning, but more importantly, it can save huge heat - treatment costs and effectively reduce the production cost. Crankshaft residual heat normalizing with alloying to replace the current normalizing heat - treatment has become an inevitable development trend in crankshaft production.
Conclusion
The iron mold coated sand crankshaft casting simplifies the clay sand process, overcomes the inherent weaknesses of clay sand (huge sand treatment, dirty and poor working environment, and low material performance), can realize continuous and controllable production, and provides favorable conditions for the mechanization and automation of high - quality crankshaft production. This advanced process will surely be more and more widely applied in casting production.