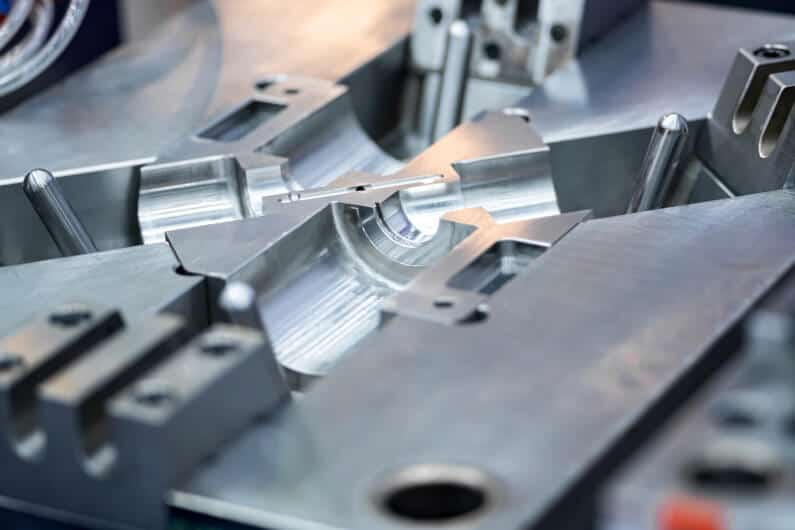
Aluminum alloy die castings are widely used in modern manufacturing due to their excellent mechanical properties. They play a crucial role in industries such as automotive, electronics, home appliances, and aerospace. However, after being produced, aluminum alloy die castings may develop mold over time, which not only affects their appearance but also may compromise product quality. This article will explore the reasons why aluminum alloy die castings mold and provide effective prevention measures to help you maintain the good condition of the castings.
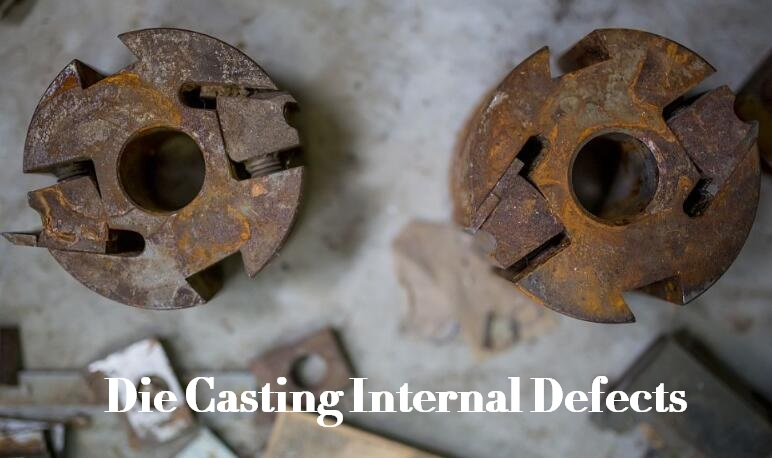
1. Why Do Aluminum Alloy Die Castings Mold?
Although aluminum alloy die castings undergo processes like cooling, cleaning, and polishing after production, they may still develop mold after being stored for a period. The main reasons include:
1.Moisture and Humid Environment
Aluminum alloy itself is a metal that is prone to reacting with moisture, especially in humid environments. If the aluminum alloy die casting is exposed to moisture in the air during storage, a thin layer of moisture may form on the surface. Under the influence of this moisture and the surrounding environment, microorganisms can proliferate, leading to mold growth.
2.Incomplete Surface Cleaning
After casting, aluminum alloy die castings typically undergo cleaning and surface treatment (such as removing oxide layers, oils, etc.). However, if the cleaning is not thorough, any remaining moisture or oil residues can become a breeding ground for mold, which leads to the molding issue.
3.Improper Storage Conditions
If die castings are stored in places with poor ventilation and excessive humidity, moisture can accumulate on the surface, encouraging mold and other microorganisms to grow. Particularly in warehouses or storage areas with high humidity, aluminum alloy surfaces can easily absorb moisture from the air.
4.Inadequate Surface Treatment
If aluminum alloy die castings do not undergo proper corrosion protection treatments, such as coating or anodizing, the metal surface may react with the oxygen and moisture in the air, forming an oxide layer. This environment encourages mold growth.
2. How to Prevent Aluminum Alloy Die Castings from Molding?
To prevent aluminum alloy die castings from molding during long-term storage, it is necessary to take effective measures to improve storage conditions, optimize surface treatments, and implement proper moisture and mold prevention techniques. Here are some practical prevention measures:
1.Ensure Thorough Surface Cleaning
Aluminum alloy die castings need to be thoroughly cleaned after production. It is essential to remove any oil residues, dirt, and moisture, especially after cleaning and polishing. The castings should be dried using drying equipment or desiccants to eliminate any remaining moisture on the surface.
2.Choose Appropriate Storage Conditions
The storage environment for die castings should be dry, clean, and free from excessive humidity. The ideal storage conditions should include good ventilation, preventing direct exposure to humid air. The humidity in the storage area should be kept within an appropriate range, generally below 50%. Additionally, castings should not be exposed to rain or high-humidity environments for prolonged periods.
3.Use Moisture-Proof Packaging
When storing aluminum alloy die castings, moisture-proof packaging can effectively prevent moisture from reaching the surface of the castings. Using moisture-proof bags, desiccant packets, or moisture-resistant packaging materials can reduce the impact of moisture on the castings, especially during transportation and long-term storage.
4.Apply Surface Corrosion Protection
Surface treatments, such as anodizing, coating, or corrosion-resistant coatings, can significantly enhance the resistance of aluminum alloy die castings to corrosion. These treatments form a protective layer on the surface, reducing direct exposure of the metal to moisture and preventing mold growth. Anodizing not only enhances corrosion resistance but also forms a protective layer that prevents surface oxidation.
5.Use Mold Inhibitors
Consider applying a mold inhibitor or anti-mold coating to the surface of aluminum alloy die castings. These coatings can effectively suppress the growth of mold and minimize the impact of moisture on the castings. Many specialized mold-resistant coatings for metal surfaces are available, which form a protective film on the surface to prevent moisture infiltration.
6.Regularly Inspect Storage Conditions
It is important to regularly inspect the storage environment and the condition of the die castings to detect any signs of mold growth. For die castings stored for a long time, periodic drying or the use of dehumidifiers can help reduce moisture levels in the storage area.
3. Conclusion
Aluminum alloy die castings are widely used across various industries due to their excellent mechanical properties. However, if the storage environment is too humid, surface cleaning is inadequate, or surface treatments are not applied correctly, mold can develop on the castings. By taking measures such as ensuring thorough surface cleaning, improving storage conditions, using moisture-proof packaging, applying surface treatments, and using mold-resistant coatings, it is possible to effectively prevent aluminum alloy die castings from molding. These preventative methods not only help extend the service life of the castings but also improve the market competitiveness of the products.
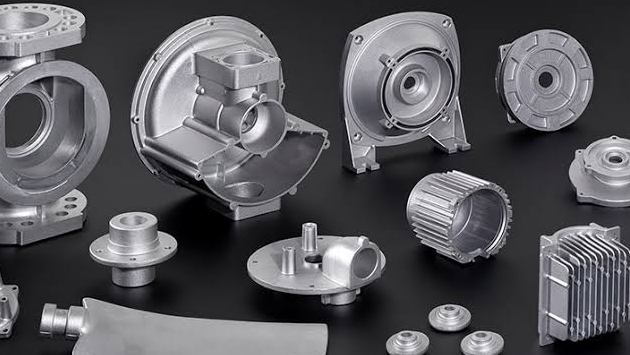