What is 3d printer sand casting?
2025-01-06 15:36:41 hits:0
The Application of 3D Printing in Sand Casting
In today's rapidly developing manufacturing field, sand casting, as a traditional and well-established process, is deeply integrating with the cutting-edge 3D printing technology, opening up a brand-new chapter of transformation.
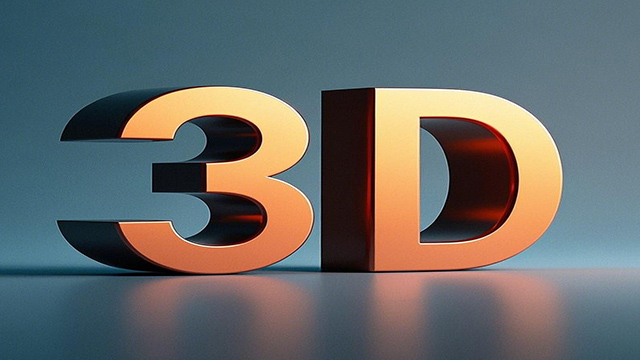
I. The Dilemmas and Challenges of Traditional Sand Casting
For a long time, sand casting has relied on manual or conventional mechanical molding to produce molds. According to industry statistics, the production efficiency of traditional manual molding is usually only a few to a dozen pieces per hour, far below the requirements of modern automated production lines. Moreover, the precision of manual molding can generally only be controlled within about ±1mm, making it difficult to meet the production of products with strict precision requirements, such as precision instrument components. Although mechanical molding improves efficiency to a certain extent, in the face of complex and changeable casting designs, the mold development cycle often lasts for several weeks or even months. Take a certain auto parts foundry as an example. The development of a new type of engine block mold took nearly three months from design to final delivery and cost as high as 500,000 yuan. Once the product design changes, the original mold is basically scrapped, resulting in huge waste. In addition, there are bottlenecks in optimizing the internal structure of molds made by traditional methods. The proportion of loose areas inside the sand molds produced by traditional processes can reach 10% - 15%, seriously affecting the improvement of casting quality.
II. The Principle and Advantages of 3D Printing Technology
3D printing, also known as additive manufacturing, builds three-dimensional entities by layering materials based on digital models. In the application of sand casting, its working principle is to layer and solidify specially prepared sand materials, such as sand grains bonded with photosensitive resin or sand powder mixed with hot-melt adhesives, according to a preset computer model.
Compared with traditional methods, 3D printing brings many advantages to sand casting. Firstly, the design freedom is greatly enhanced, enabling the easy production of molds for castings with complex internal cavities, thin walls, and irregular shapes that are difficult to achieve with traditional techniques, such as the complex cooling channel sand molds for aero-engine blades, where the narrowest part of the channel can be less than 2mm, opening up new paths for the development of high-performance castings. Secondly, it shortens the product development cycle. There is no need for a long mold manufacturing process, and design modifications can be immediately reflected in the printed model for rapid iteration. According to the feedback from a certain aerospace component R & D enterprise, after adopting 3D printed sand casting, the cycle from design to the completion of the first prototype was shortened from an average of 6 months to within 4 months, with an efficiency improvement of over 30%. Thirdly, it reduces costs, especially for small-batch and customized production. It eliminates the high cost of molds and precisely prints sand materials according to actual needs, reducing waste. Take a certain high-end customized machinery product manufacturer as an example. For small-batch production of 50 special structure castings, if traditional mold casting is used, the unit cost after mold cost allocation is as high as 2,000 yuan, while 3D printed sand casting only requires 800 yuan, with a cost reduction of 60%.
III. Innovations of 3D Printing in Each Link of Sand Casting
(I) Pattern Making Process
In the past, patterns were mostly made from wood, metal, etc., and the production process was cumbersome and the precision was limited. Nowadays, 3D printing can directly print high-precision patterns based on CAD models. The dimensional accuracy can reach ±0.1mm or even higher, and the surface quality is fine, perfectly replicating the design intent, providing an accurate foundation for subsequent molding. Moreover, the pattern parameters can be quickly adjusted to meet the requirements of different castings. For example, a certain precision foundry reduced the scrap rate caused by pattern precision problems from 8% to within 2% through 3D printed patterns.
(II) Molding Process
Replacing traditional molding methods such as ramming and mechanical compaction, 3D printing directly forms sand molds. The internal sand grains are evenly distributed and the compactness is consistent, ensuring the stability of the metal liquid flow during pouring and reducing defects caused by turbulence. Research data from a certain casting laboratory shows that the standard deviation of the internal sand grain compactness of 3D printed sand molds is reduced by 50% compared with that of traditional mechanical molding. It can accurately design the positions and shapes of gates and risers to optimize the paths of metal liquid supply and gas exhaust, improving the yield rate of castings. Take the heavy machinery castings produced by a certain large foundry as an example. After adopting 3D printed sand molds, the yield rate increased from 70% to 85%.
(III) Melting and Pouring Process
Thanks to the high precision and optimized structure of 3D printed sand molds, the melting process can more accurately adjust the composition and temperature of the metal liquid according to the casting requirements. During pouring, the metal liquid fills smoothly in the ideal cavity environment, reducing the probability of defects such as sand holes and cold shuts, and improving the consistency and reliability of casting quality. Experimental data from a certain iron and steel research institute shows that the frequency of defects such as sand holes and cold shuts in castings produced by 3D printed sand casting is reduced by 40% - 50% compared with that of traditional sand casting.
(IV) Sand Cleaning Process
Due to the certain characteristics of 3D printed sand mold materials, the sand cleaning work is relatively simplified. Some binders lose their adhesiveness after high-temperature pouring, making the molding sand easier to fall off, reducing the labor intensity and time cost of sand cleaners and improving production efficiency. Statistics from a certain casting workshop show that after adopting 3D printed sand molds, the sand cleaning time was shortened by an average of 30%, and the number of sand cleaners could be correspondingly reduced by 20%.
IV. Application Cases and Practical Results
In the aerospace field, key components of a certain model of aircraft adopted 3D printed sand casting technology and successfully produced aluminum alloy castings with complex cooling structures inside. While ensuring strength, the weight was effectively reduced. After testing, the weight was reduced by 15%, and the research and development cycle was shortened by more than 30%, contributing to the performance improvement of the aircraft. In the automotive manufacturing industry, during the trial production stage of engine blocks, 3D printed sand molds were used to quickly verify the design feasibility and save mold costs of hundreds of thousands of yuan. Take the development of a certain new car model as an example. The mold cost was saved by up to 300,000 yuan, accelerating the launch of the new car model.
V. Problems Faced and Future Prospects
Although 3D printing shows great potential in sand casting, it still faces challenges. On the one hand, the cost of 3D printing equipment and materials is relatively high. Currently, the price of mainstream industrial-grade 3D printing equipment on the market ranges from 500,000 yuan to 2 million yuan, and the price of special sand mold materials is also dozens to hundreds of yuan per kilogram, limiting the large-scale application of small and medium-sized enterprises. On the other hand, the printing speed is relatively slow, and for large-scale mass production, the efficiency needs to be further improved. However, with technological progress, the equipment price will continue to decline and the printing speed will increase. It is expected that within the next five years, the equipment price will be reduced by 30% - 50%, and the printing speed will be increased by 2 - 3 times. 3D printing is expected to become the mainstream technology in sand casting, complementing traditional processes and promoting the casting industry to a higher level, providing stronger technical support for industries such as high-end equipment manufacturing and new energy, and shaping a more brilliant future for the manufacturing industry.
Do you have a demand for customized ductile iron components? Click here to contact us directly, and our professional team will provide you with personalized solutions and high-quality castings.