What is Casting Cleaning in the Foundry Industry?
2025-01-03 14:14:13 hits:0
I. Importance and Background of Casting Cleaning
In the complex and delicate industrial process of casting, casting cleaning is an indispensable and crucial step. After the casting solidifies and is removed from the mold, its surface is often attached with numerous superfluous substances that affect the casting quality and subsequent use, and thus casting cleaning operations are required.
II. Objects of Casting Cleaning
Simply put, casting cleaning is to remove excess parts such as molding sand, oxide scale, and gates and risers on the casting surface.
(I) Necessity of Molding Sand Cleaning
As a key material used to construct the mold during the casting process, part of the molding sand will adhere tightly to the casting surface after the casting is formed. If not removed, it will not only affect the appearance of the casting but also may cause problems such as wear and jamming during subsequent machining or use. For example, after the casting of an automobile engine block is completed, if the molding sand remains, during engine operation, the molding sand particles may enter between the piston and the cylinder wall, exacerbating wear and reducing the engine life.
(II) Significance of Oxide Scale Cleaning
Oxide scale is a dense oxide film generated by the chemical reaction between the metal and the oxygen in the air during the high-temperature melting, pouring, and subsequent cooling processes of the casting. This layer of oxide scale not only makes the casting appearance rough and dull but also may conceal minor defects of the casting, such as microcracks, bringing difficulties to subsequent quality inspection. Meanwhile, in some application scenarios with high requirements for surface quality, such as the casting of precision instrument housings, the existence of oxide scale is absolutely unacceptable.
(III) Importance of Gate and Riser Cleaning
Gates and risers are the key objects of casting cleaning. The gate is the channel through which the liquid metal flows into the mold, and the riser is used to supplement the liquid metal when the casting solidifies to prevent shrinkage porosity and cavities. But after the casting is formed, they have completed their missions and become superfluous parts. If the gates and risers are not removed, on the one hand, it will increase the casting weight, resulting in unnecessary material waste; on the other hand, for some castings with assembly requirements, such as mechanical connectors, the protruding gates and risers will affect the assembly accuracy and even make normal assembly impossible.
III. Technological Means of Casting Cleaning
To achieve effective casting cleaning, a variety of technological means are involved.
(I) Sand Knocking Process
Sand knocking is a relatively traditional and commonly used method. Workers hold tools and gently tap the casting to make the loosely attached molding sand fall off. However, this method has relatively low efficiency and is difficult to clean thoroughly for some castings with complex shapes.
(II) Grinding Process
Grinding is often used to remove the oxide scale and the small amount of residual molding sand on the casting surface. Through tools such as grinding wheels and sandpaper, the casting surface is ground smooth. However, during the grinding process, attention should be paid to controlling the force and temperature to avoid damaging the casting body.
(III) Cutting Process
Cutting is often used to remove gates and risers. According to the casting material and the size of the gates and risers, appropriate cutting tools are selected. For example, for the gates and risers of small cast iron castings, a manual cutting saw can be used, while for the gates and risers of large steel castings, efficient cutting methods such as flame cutting and plasma cutting are required.
IV. Summary of Casting Cleaning
In conclusion, as the final step of the casting process, casting cleaning seems simple but actually plays a vital role in ensuring the casting quality and meeting subsequent use requirements. It enables the casting to enter various application fields in a perfect state through a series of fine operations.
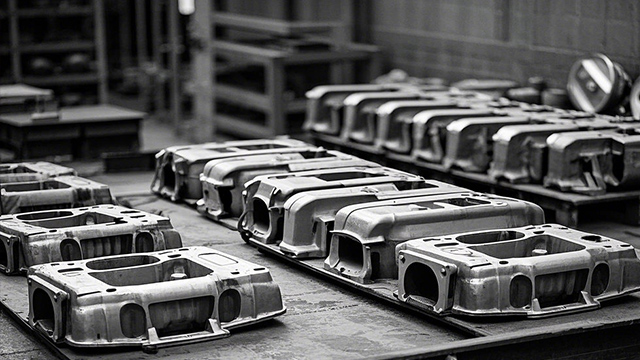