What is a Riser in the Foundry Industry?
2025-01-03 14:02:21 hits:0
I. Definition and Appearance Characteristics of Risers
In the foundry industry, a riser is a component that plays an important role in ensuring the quality of castings and is one of the key links in achieving high-quality casting formation.
Essentially, a riser is an additional liquid storage container set at specific parts of the mold. Common positions include the top of the mold or areas close to where shrinkage cavities and porosity are likely to occur in the casting. Its appearance comes in various shapes, such as regular cylindrical and square shapes, as well as irregular ones. The size of the riser is not randomly determined but precisely planned based on the size, type (small, medium, large), structural complexity of the casting, and the characteristics of the metal material used.
(I) Specifications of Risers for Small and Simple Castings
Generally, for small and simple castings, the diameter of the riser may be between 2 - 5 cm, and the height may be between 3 - 8 cm.
(II) Specifications of Risers for Medium Castings
For medium castings, the diameter range of the riser is usually between 5 - 15 cm, and the height is between 8 - 20 cm.
(III) Specifications of Risers for Large and Complex Castings
For large and complex castings, such as the casting of the cylinder block of a large ship engine, the diameter of the riser can reach more than 30 cm, and the height can exceed 50 cm.
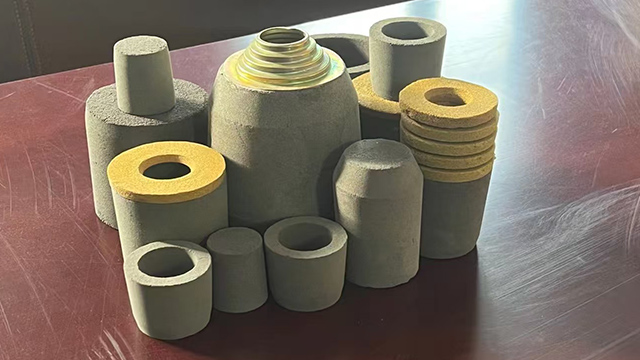
II. Functional Principle of Risers
Explaining from the functional principle aspect, risers undertake a crucial task during the solidification process when the casting changes from liquid to solid. After the liquid metal is poured into the mold, as the temperature drops, the metal begins to solidify and contract.
(I) Solidification Shrinkage Rates of Different Metals
Taking common gray cast iron as an example, its solidification shrinkage rate is about 1% - 3%, while that of cast steel is even higher, reaching 3% - 7%. Without a riser, the last solidifying part of the casting will inevitably produce shrinkage cavities or porosity due to the lack of liquid metal supplementation.
(II) Impact of Shrinkage Cavities and Porosity on Mechanical Properties
These internal defects will significantly reduce the mechanical properties of the casting. For example, the strength may be reduced by 20% - 30%, and the toughness may be decreased by 30% - 50%, making the casting unable to meet the quality standards for practical applications. The liquid metal stored in the riser will flow continuously into the casting during the solidification and contraction stage of the casting, filling the voids caused by contraction and ensuring the compact structure of the entire casting.
III. Application of Risers in Actual Production
In actual foundry production scenarios, for different types of castings, there are strict requirements for the design and layout of risers.
(I) Case of Casting an Automobile Engine Cylinder Head
For example, in the automotive manufacturing field, when casting an automobile engine cylinder head, due to the complex air passages and oil passages inside the cylinder head, engineers use professional simulation software to accurately calculate the solidification time and shrinkage amount of different parts. After measurement, the solidification time of some key hot spots in the cylinder head needs to be controlled within 10 - 15 minutes, and the shrinkage amount should be maintained at 5 - 8 ml. Based on this, the number of risers is accurately determined to be 3 - 5, and the positions are distributed around the top of the cylinder head and the areas where the wall thickness changes abruptly. The size is finely adjusted according to the above calculation results to ensure that during the solidification of the cylinder head, the risers can timely supplement liquid metal to the key parts, meeting the strict requirements for the strength, sealing performance, and other properties of the cylinder head when the engine is running.
IV. Material Selection of Risers
There is also particularity in the material selection of risers. In most cases, the riser and the casting use the same basic metal material, which can ensure consistency in key properties such as solidification characteristics and heat conduction, enabling a smooth feeding process. However, in some special working conditions, in order to optimize the feeding effect, riser materials with special solidification characteristics will be used.
(I) Case of Casting Aerospace Components
For example, when casting some aerospace components with extremely high requirements for internal quality, exothermic riser materials are used. During the solidification process, they can release heat, extending their own solidification time by 2 - 3 times. Compared with ordinary risers, the feeding time for the casting is increased by 15 - 20 minutes, greatly enhancing the compactness of the casting and ensuring that the product quality meets the high standards of the aerospace field.
V. Development of Riser Technology
With the continuous progress of foundry technology, riser technology is also constantly evolving. In the early stage, risers were designed based on experience, and the scrap rate was relatively high, about 10% - 15%. Nowadays, with the help of digital and intelligent means and through computer simulation, the effect of risers can be accurately predicted before the actual production of castings, and parameters can be optimized and adjusted in advance.
(I) Case of an Advanced Foundry Enterprise
For example, after an advanced foundry enterprise adopted new riser design technology, the scrap rate was reduced to 3% - 5%, and the production efficiency was increased by 20% - 30%, effectively promoting the foundry industry to move towards a higher level of sophistication.
In conclusion, as a key component of the casting process, risers are of great significance in ensuring the quality of castings. The precise setting of each parameter and the continuous upgrading of technology all embody the professional wisdom of foundry engineers, laying the foundation for various industries to produce solid and reliable metal castings.