What are the Common Casting Defects and Solutions during the Casting Process?
2025-01-03 13:46:55 hits:0
In the complex and delicate casting process of the foundry industry, despite the efforts of craftsmen to achieve perfection, some casting defects still frequently occur due to numerous variables and procedures involved. Understanding these common problems and their corresponding solutions is crucial for improving casting quality and reducing the scrap rate.
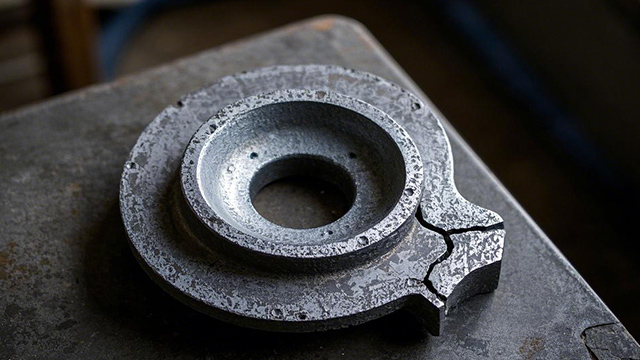
I. Sand Holes
Sand holes are one of the more common defects, manifested as scattered or dense small holes on the surface or inside of the casting, filled with molding sand particles. The main causes stem from the mold: on the one hand, the strength of the molding sand is insufficient. Under the impact and erosion of the molten metal, the molding sand is likely to fall off and mix into the molten metal, ultimately forming sand holes. For example, in some small foundries, in order to save costs, low-quality molding sand with a small amount of binder and far below-standard strength is selected, resulting in frequent sand holes. On the other hand, the compactness of the mold is uneven. Local loose areas are easily broken through by the molten metal during casting, entraining the molding sand to form sand holes.
Solutions: Firstly, ensure the quality of the molding sand. Select high-quality raw materials for the molding sand and strictly mix them according to the formula to guarantee sufficient strength. Generally, the compressive strength of the molding sand can be monitored. For example, in ordinary sand casting, the compressive strength of the molding sand needs to reach 0.3 - 0.5 MPa. At the same time, during the molding process, adopt appropriate compacting methods, such as mechanical jolting and compaction, to ensure the uniform compactness of all parts of the mold. For large casting molds, high-pressure compaction is often used to control the compactness deviation within a very small range, effectively reducing sand hole defects.
II. Gas Holes
Gas holes appear as circular, elliptical, or irregular cavities inside the casting, usually filled with gas. There are two main causes: one is that the molten metal absorbs gas during the melting process. For example, when melting aluminum alloys, if the melting environment has high humidity, the molten metal will absorb a large amount of hydrogen. When the casting solidifies, the gas cannot escape and forms gas holes; the second is the poor permeability of the mold. The gas generated by the cooling and solidification of the molten metal is difficult to discharge and accumulates inside the casting to form gas holes. There was once a foundry that produced cast iron pipe fittings. Due to the substandard permeability of the molding sand, the gas hole defect rate was once as high as 20%, seriously affecting product quality.
Solutions: To address the problem of gas absorption by the molten metal, a refining degassing process can be adopted during melting. For example, inert gas argon can be introduced into the aluminum alloy melt. The rising bubbles carry out the hydrogen, reducing the gas content in the molten metal to the qualified range. For the permeability problem of the mold, optimize the molding sand formula to increase the permeability of the molding sand. For example, add an appropriate amount of wood chips and other permeability modifiers to the molding sand. At the same time, reasonably set up exhaust channels, such as opening exhaust holes or using exhaust pins on the mold to ensure the smooth discharge of gas and effectively control gas hole defects.
III. Incomplete Filling
Incomplete filling refers to the phenomenon that the casting is not completely filled with the molten metal, resulting in local lack of material. This is usually caused by too slow a casting speed or too low a casting temperature. When the casting speed is slow, the molten metal loses heat quickly during the flow process, and its fluidity deteriorates, unable to reach all corners of the cavity; when the temperature is too low, the fluidity of the molten metal itself is poor and it is difficult to fill complex cavities. This defect is particularly likely to occur when casting some thin-walled, complex-structured precision castings.
To solve the problem of incomplete filling, it is necessary to precisely control the casting speed and temperature. For different metals and castings, appropriate casting parameters should be determined based on experience and experimental data. For example, when casting thin-walled copper alloy parts, the casting speed can be 10% - 20% faster than that of ordinary castings, and the temperature can be controlled 30°C - 50°C higher than the conventional casting temperature of copper alloys to ensure that the molten metal has sufficient fluidity and impact force to completely fill the cavity and avoid incomplete filling.
IV. Cold Shut
The characteristic of cold shut is that a linear gap that is not completely fused appears on the surface of the casting, as if the molten metal is divided into two or more streams and does not merge well. The main reasons are that the pouring temperature of the molten metal is too low, so that when the various streams of molten metal meet, they cannot achieve good fusion due to the low temperature; or the casting process is interrupted, resulting in a large temperature difference between the front and rear injected molten metals and they cannot be integrated. When casting in a low-temperature environment in winter, the probability of cold shut defects will increase significantly.
Solutions: It is necessary to strictly control the casting temperature and make appropriate adjustments according to the environmental temperature and casting characteristics. For example, in the cold season, the casting temperature of aluminum alloys can be increased by 20°C - 30°C; at the same time, optimize the casting process to ensure that the casting process is continuous and stable and avoid pauses, reducing cold shut defects and ensuring the appearance and internal quality of the casting.
V. Shrinkage Cavities and Porosity
Shrinkage cavities are large holes formed in the last solidifying part of the casting during the solidification process because the liquid shrinkage and solidification shrinkage do not get sufficient liquid metal supplementation; porosity refers to a group of scattered, small holes around the shrinkage cavity. This is related to the solidification characteristics of metals. Some alloys undergo mushy solidification. The liquid metal in the mushy zone cannot be effectively fed, so shrinkage cavities and porosity are likely to occur. For example, steel castings are more prone to such defects than cast iron castings because of their wide solidification range.
To address this defect, the riser feeding process can be adopted. Set risers at the parts of the casting where shrinkage cavities are likely to appear. The molten metal in the risers solidifies last, using its liquid metal to supplement the shrinkage of the casting. At the same time,with the use of chills to accelerate the local cooling speed of the casting, guide the solidification sequence, transfer the shrinkage cavities and porosity to the risers, and finally remove the risers to obtain a dense casting.
In conclusion, the casting defects in the casting process need to comprehensively investigate the causes from aspects such as raw materials, process parameters, and molds, and take targeted solutions. Through continuous optimization and fine control, high-quality, defect-free castings can be produced to meet the needs of various industries for metal products.