What is Molding Sand in the Foundry Industry?
2025-01-02 16:35:50 hits:0
In the foundry industry, molding sand is a crucial basic material that plays a decisive role in the final quality of castings.
I. Definition and Basic Properties of Molding Sand
By definition, molding sand is the material used to make molds. It is not a simple and random combination of sands but a special mixture with strict performance requirements.
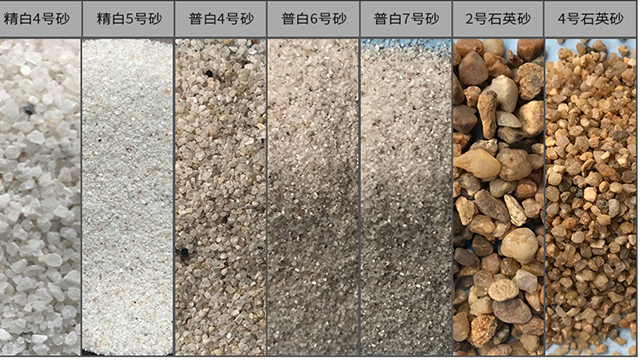
(I) Strength Requirement
Firstly, molding sand must possess certain capabilities to withstand the impact and pressure brought by the injection of molten metal and not collapse or deform during this process. Generally, for the molding sand used in ordinary small and medium-sized castings, its compressive strength needs to reach around 0.3 - 0.5 MPa, so as to ensure that the mold maintains a stable shape and provides a reliable space for the solidification and forming of the molten metal.
(II) Permeability Index
Permeability is also one of the key performance indicators of molding sand. During the cooling and solidification of the molten metal, a large amount of gas will be generated. If the permeability of the molding sand is not good, these gases cannot be discharged smoothly and will be trapped inside the casting, forming porosity defects. For example, a foundry was producing a batch of automobile engine block castings. Initially, due to the substandard permeability of the molding sand, which was only 50 - 70 air holes per square centimeter, it was found during the finished product inspection that more than 30% of the engine blocks had pores of different sizes inside, severely affecting the quality and performance of the blocks and resulting in a large number of scrapped products. Later, after adjusting the molding sand formula and increasing the permeability to 100 - 120 air holes per square centimeter, the porosity defect rate of the subsequently produced engine blocks was significantly reduced to within 5%.
(III) Refractoriness Points
Refractoriness cannot be ignored either. During the casting process, the temperature of the molten metal is extremely high. For example, when casting iron and steel castings, the temperature of the molten iron can often reach around 1500 °C. If the molding sand has poor refractoriness, it will be easily melted and sintered at high temperatures, and then adhere to the surface of the casting, destroying the surface quality of the casting. Taking the casting of automobile wheels as an example, if the refractoriness of the molding sand is insufficient, defects such as sand holes and sand sticking will appear on the surface of the wheel, not only affecting the appearance but also possibly reducing the strength and reliability of the wheel. According to industry statistics, the scrap rate of castings caused by the problem of molding sand refractoriness can even reach up to 20% in some small foundries.
II. Practical Application Scenarios of Molding Sand
In practical applications, quartz sand is one of the common raw materials for molding sand. It has the advantages of wide sources and relatively low cost. However, different castings have very different specific requirements for molding sand due to their own characteristics.
(I) Requirements for Large Castings
For large castings, such as the engine blocks of ship engines, due to their huge size, the molding sand needs higher strength to support the entire mold structure. Usually, special binders will be added on the basis of quartz sand to enhance the bonding strength of the molding sand to prevent the mold from collapsing during the casting process.
(II) Considerations for Precision Castings
For some precision castings, such as aero-engine blades, in addition to having high requirements for the strength, permeability, and refractoriness of the molding sand, it is also required that the molding sand has good collapsibility, so that the molding sand can be easily removed after the casting is formed without damaging the precise blade structure.
III. The Issue of Reusing Molding Sand
In addition, the reuse of molding sand is also a focus of foundries. A reasonable molding sand recycling process can reduce production costs. However, as the number of reuse times increases, the performance of the molding sand will gradually decline, such as a decrease in strength and permeability. Some advanced foundries will regularly test the performance of the molding sand and adjust the molding sand formula by adding an appropriate amount of new sand and binders according to the test results, so that the molding sand can be reused multiple times while ensuring the stable quality of the castings.
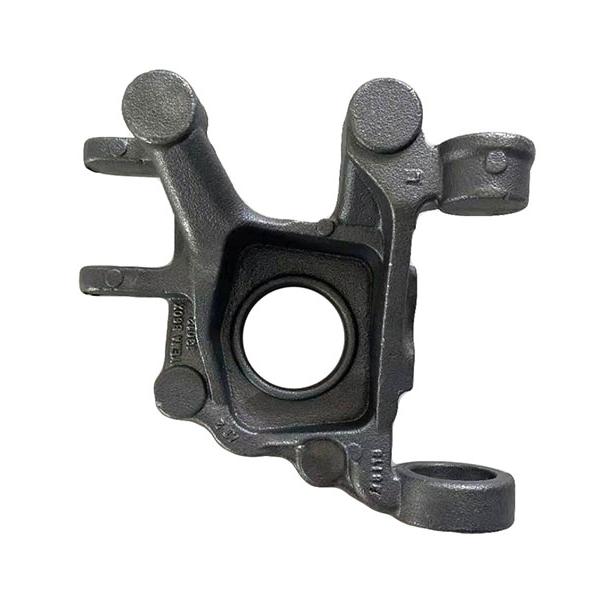
IV. Summary
In conclusion, molding sand is the cornerstone of the foundry industry. The quality of its performance directly relates to the quality, production cost, and production efficiency of castings. Foundry enterprises must have an in-depth understanding of the characteristics of molding sand and optimize the molding sand formula and application process according to the requirements of different castings in order to gain a foothold in the fierce market competition and produce high-quality castings. If you want to learn more about the foundry industry, such as What is Spheroidizing Treatment , What is Inoculation Treatment, please click it to view, and a vast amount of professional content awaits your exploration.
Furthermore, if you have a need for custom ductile iron components, click here to directly contact us. Our professional team will provide you with personalized solutions and high-quality services.