Ductile Iron Makes Car Parts More Durable
2025-01-02 13:43:23 hits:0
In today's booming automotive industry, consumers have increasingly higher requirements for the quality and durability of automobiles. As key components of automobiles, the durability of car parts directly affects the performance and service life of the entire vehicle. Ductile iron, a material with outstanding properties, is quietly triggering a durability revolution in the field of car parts. In another article of ours, we delved into what ductile iron is. Click here to learn more.
Advantages of Ductile Iron over Traditional Materials
Traditional materials for car parts often reveal many shortcomings when facing complex and changeable driving environments. Take the engine block as an example. Under high temperature, high pressure, and frequent vibration impacts, ordinary cast iron engine blocks are prone to cracks, deformations, and other problems, leading to a decline in engine performance and even frequent failures. However, the emergence of ductile iron has changed this situation. After special spheroidizing treatment, the graphite spheres are evenly distributed in the matrix, effectively reducing stress concentration and greatly enhancing the strength and toughness of the material. This enables the engine block made of ductile iron to withstand more severe working conditions, ensuring the stable operation of the engine while significantly extending its service life. According to relevant data, compared with ordinary cast iron engine blocks, the overhaul cycle of engines with ductile iron engine blocks can be extended by 30% - 50%, saving car owners a lot of maintenance costs and time.
Ductile Iron Improves the Performance of the Vehicle Chassis Suspension System
Looking at the vehicle chassis suspension system, it is an important component related to the vehicle's handling stability and ride comfort. In the past, some suspension components were made of ordinary steel. During long-term driving on bumpy roads and frequent loading processes, they were prone to wear, fatigue fractures, and other situations. Ductile iron, with its excellent wear resistance and outstanding fatigue resistance, has brought a qualitative improvement to the suspension system. The graphite spheres in ductile iron endow the material with good self-lubricating properties, reducing the friction coefficient between components and reducing wear. At the same time, its unique microstructure enables it to remain stable under repeated alternating loads, effectively avoiding fatigue failure. For example, the lower control arm made of ductile iron, after undergoing rigorous durability tests, had about 40% less wear than components made of ordinary steel, and it could still remain intact in a fatigue test simulating a driving mileage of 1 million kilometers, providing a solid guarantee for the safe driving of the vehicle.
Ductile Iron for Automobile Wheels
The application of ductile iron in automobile wheels is also one of the areas where it shines. The wheel not only has to bear the weight of the vehicle body but also withstand the centrifugal force generated during high-speed driving and road impacts. Although ordinary aluminum alloy wheels are lighter in weight, they are relatively weak in strength and durability and are prone to deformation, cracking, and other problems. Ductile iron wheels, on the other hand, combine high strength and good toughness and can easily cope with various road conditions. Whether on rugged mountain roads, potholed country lanes, or driving at high speed on the highway for a long time, ductile iron wheels can work stably and reliably. A market research found that, under normal use conditions, the replacement cycle of wheels on vehicles using ductile iron wheels can be extended by 2 - 3 years compared with that of aluminum alloy wheels, greatly reducing the operating costs for car owners.
Application of Ductile Iron in Other Core Components
In addition, ductile iron also plays an important role in core components such as the braking system and transmission of automobiles. The brake disc made of ductile iron, with its excellent thermal stability, high strength, and wear resistance, ensures the stable and reliable braking performance, reducing potential safety hazards caused by brake disc wear or deformation; if the gears in the transmission are made of ductile iron, their precise transmission characteristics and high load-carrying capacity make the transmission shift more smoothly and have a longer service life.
From the source of automobile production, major automobile manufacturers are also paying more and more attention to the application of ductile iron in component manufacturing. They are constantly increasing their R & D investment and optimizing the production process of ductile iron to further improve its performance and meet the growing demands of the automotive industry. At the same time, the automotive parts repair market also benefits from the wide application of ductile iron. Repair technicians have found that after using ductile iron parts for repairs and replacements, the vehicle's return repair rate is significantly reduced, and customer satisfaction is greatly improved.
For detailed introductions of Automotive parts castings, click here to consult.
Furthermore, if you have a need for custom ductile iron components, click here to directly contact us. Our professional team will provide you with personalized solutions and high-quality services.
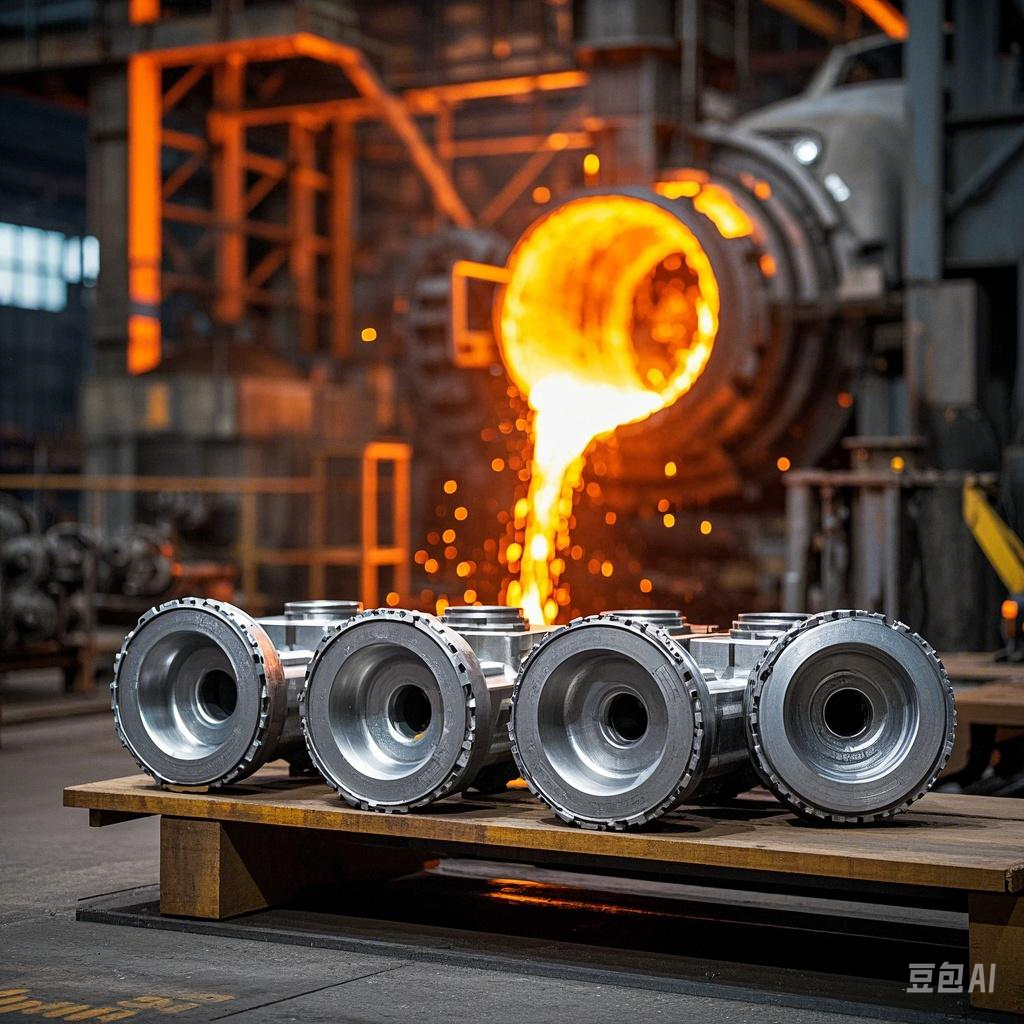