Malleable Iron vs Cast Iron
2024-12-27 09:48:21 hits:0
Malleable Iron and Cast Iron: The Twins of Materials Science and Their Distinct Glories
In the progression of human civilization, the development of materials science has always been a pivotal force in advancing social productivity. Among the myriad metallic materials, cast iron and its derivative, malleable iron, stand out with their unique properties and wide application fields, becoming indispensable components in the field of industrial manufacturing. This article aims to explore the basic characteristics, production processes, performance differences, and respective applications of malleable iron and cast iron, while presenting data and case studies to shed light on these two materials.
Cast Iron: The Ancient and Resilient Foundation Material
Cast iron, primarily composed of iron, carbon, and silicon, is obtained through blast furnace smelting and then shaped through casting processes. Its tensile strength typically ranges from 150 to 400 MPa, with a yield strength between 200 and 300 MPa. Its elongation is very low, generally between 0.01% and 0.5%, and its impact toughness is poor. However, cast iron is widely used in machinery manufacturing, automotive components, piping systems, building structures, and other fields due to its good castability, high compressive strength (especially notable in gray cast iron), and low cost. For instance, gray cast iron is often used to manufacture pipes, valves, pumps, and other fluid equipment due to its good shock absorption and castability.
Malleable Iron: The Art of Improvement and Innovation
To address the lack of toughness in cast iron, malleable iron was invented through practical experimentation. The chemical composition of malleable iron mainly includes carbon (2.2% to 2.8%), silicon (1.0% to 1.8%), manganese (0.3% to 0.8%), and small amounts of sulfur (≤0.2%) and phosphorus (≤0.1%). Its production process involves white iron casting and graphitization annealing, with graphitization annealing being the crucial step that transforms the originally brittle cast iron into a material with fine spherical graphite, significantly improving its toughness, strength, and plasticity. Depending on the annealing method, malleable iron can be classified into blackheart malleable iron, whiteheart malleable iron, and pearlitic malleable iron, each with different mechanical properties and applications.
Malleable iron exhibits superior machinability compared to gray cast iron and ductile iron, with higher mechanical properties than gray cast iron, including plasticity and toughness. For example, blackheart malleable iron has high plasticity and toughness, while pearlitic malleable iron boasts high strength, hardness, and wear resistance.
Here are some specific data and case studies on the application of malleable iron:
Shipbuilding Industry: Malleable iron, with its high strength and toughness, is commonly used in the manufacture of structural components such as anchor bases and anchor chain wheels, as well as in the production of propellers.
Construction Sector: Components made of malleable iron, such as rainwater outlets and inspection wells, enhance the durability and safety of buildings. Additionally, malleable iron is used to make important parts like bridge ball-and-socket supports and plungers, ensuring the stability and safety of structures.
Automotive Industry: Crucial components like engine blocks, crankcases, and clutches are mostly manufactured using malleable iron materials. Furthermore, malleable iron is used to produce automotive chassis and suspension parts, improving vehicle safety and operational stability.
Petrochemical, Mining, and Metallurgical Industries: High-strength piping made of malleable iron is used in petrochemical equipment, while wear-resistant balls and caps are employed as vital components in abrasive crushing processes.
Specifically, crankshafts, gears, and other parts made of malleable iron exhibit excellent strength and toughness, meeting the requirements for high strength and wear resistance in machinery. For instance, a shipbuilding company chose malleable iron as the material for anchor chain wheels when manufacturing large cargo ships. After extensive sea trials, the material proved its superior wear resistance and fatigue resistance.
Conclusion
Malleable iron and cast iron, as the "twins" of materials science, although originating from the same source, exhibit distinct performance characteristics through different processing techniques, each playing an irreplaceable role in industrial production. As technology advances, the requirements for material properties continue to increase, prompting in-depth research into the modification of cast iron and malleable iron to develop more efficient, environmentally friendly, and high-performance new cast iron materials to meet the needs of future industrial development. In this era of continuous innovation and sustainable development, the story of cast iron and malleable iron will undoubtedly continue to write new chapters in materials science.
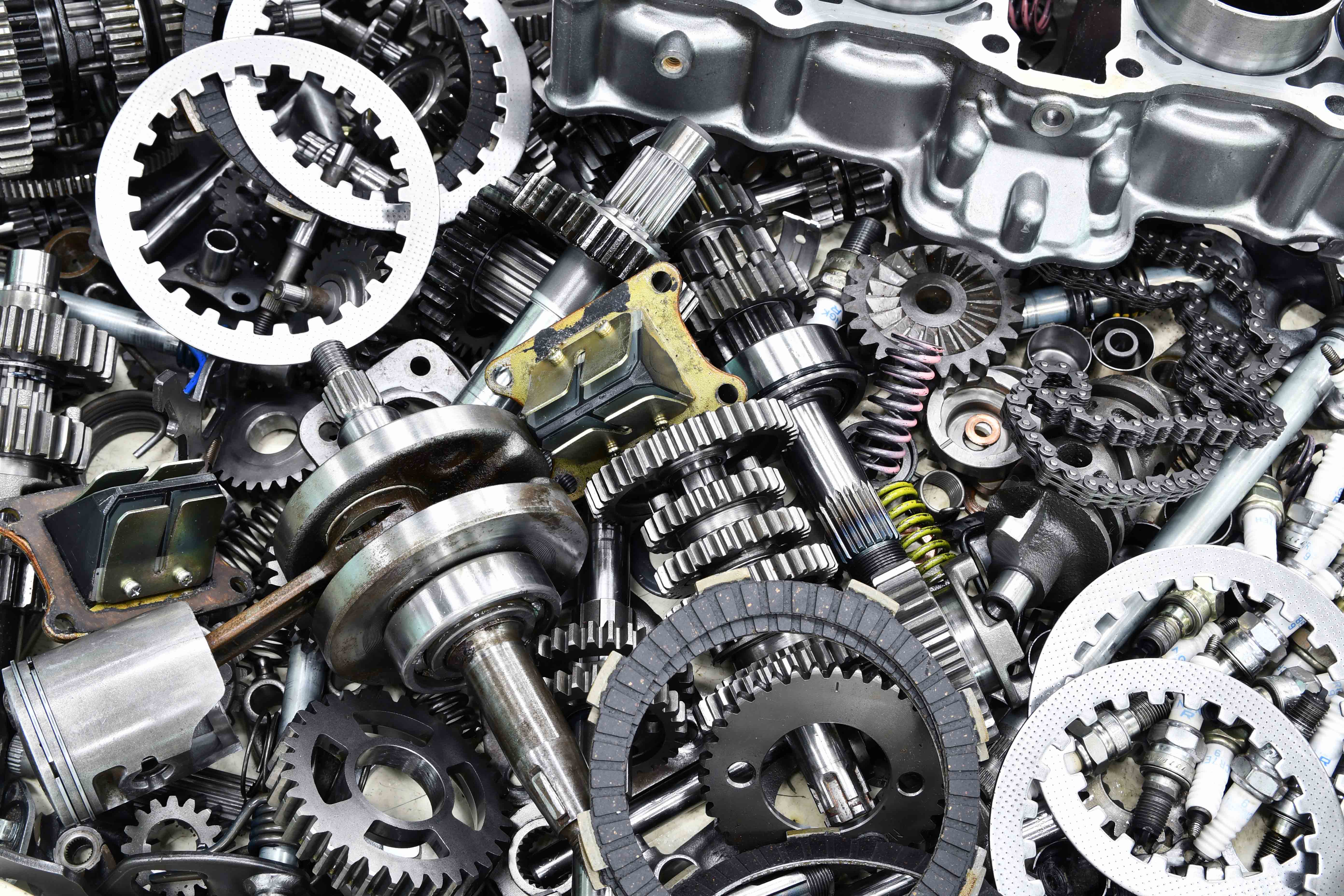