Detailed Explanation of Cast Iron Component Cost Accounting
2024-12-26 16:51:54 hits:0
In the industrial manufacturing sector, cast iron components, as indispensable basic parts, have always been the focus of cost accounting for enterprises. The cost structure of cast iron components is complex, involving raw materials, processing, labor, equipment depreciation, and other aspects. This article will provide a detailed explanation of the cost accounting method for cast iron components, combining specific data and case studies, to provide references for enterprises to optimize cost control.
I. Cost Components of Cast Iron Components
Raw Material Costs
- Primary Materials: Pig iron, scrap steel, ferrosilicon, ferromanganese, etc.
- Price Examples: Pig iron at 3150 yuan/ton, scrap steel at 2200 yuan/ton, ferrosilicon at 6500 yuan/ton, ferromanganese at 6600 yuan/ton.
- Auxiliary Materials: Auxiliary materials for molding and cleaning.
- Loss Compensation: Losses during melting and cutting, usually compensated with a coefficient of 1.1.
- Processing Costs
- Primary Materials: Pig iron, scrap steel, ferrosilicon, ferromanganese, etc.
- Casting: Including melting, pouring, cooling, and other processes.
- Heat Treatment: Such as quenching and tempering, to improve the mechanical properties of cast iron components.
- Machining: Such as cutting, drilling, grinding, etc., to meet dimensional and shape requirements.
- Energy Consumption: Electricity, fuel, etc.
- Equipment Depreciation: Depreciation costs of casting equipment, heat treatment equipment, and machining equipment.
- Labor Costs
- Wages: Basic wages, overtime pay, etc., for workers.
- Social Insurance: Pension insurance, medical insurance, work-related injury insurance, etc.
- Training Costs: Training costs to improve workers' skills.
- Other Costs
- Equipment Maintenance: Routine maintenance and repair costs of equipment.
- Quality Inspection: Quality inspection costs for raw materials and finished products.
- Management Costs: Including office expenses, travel expenses, etc.
II. Cost Accounting Methods
Direct Material Costs
- Calculate the quantity and price of raw materials required based on the formulation and process requirements of cast iron components.
- Consider raw material losses and compensation coefficients to obtain direct material costs.
- Processing Costs
- Calculate processing costs based on equipment depreciation, energy consumption, tool wear, and other expenses during casting, heat treatment, and machining processes.
- Adjust processing costs considering production efficiency and scrap rates.
- Labor Costs
- Calculate labor costs based on workers' wages, social insurance, and training costs.Adjust labor costs considering workers' productivity and hour utilization rates.
- Other Costs
- Calculate other costs based on the actual situation of equipment maintenance, quality inspection, and management expenses.
III. Case Study Analysis
Case Study 1: Cost Accounting for One Ton of Cast Iron Components Produced by a Casting Enterprise
- Raw Material Costs: Pig iron 1943.55 yuan (0.617 tons × 3150 yuan/ton), scrap steel 519.8 yuan (0.269 tons × 2200 yuan/ton), ferrosilicon 136.5 yuan (0.021 tons × 6500 yuan/ton), ferromanganese 204.6 yuan (0.031 tons × 6600 yuan/ton), minus recycling 1135.2 yuan (-0.430 tons × 2640 yuan/ton), totaling 3322.61 yuan.
- Processing Costs: Electricity costs 1150.8 yuan (1000 kWh × 0.85 yuan/kWh), polystyrene 64.8 yuan, and other processing costs (such as equipment depreciation, tool wear, etc.) allocated proportionally, totaling approximately 2000 yuan.
- Labor Costs: Calculated based on working hours, with 56.7 hours per ton of cast iron components, an annual total of 249,236 working hours, and annual wages and additions totaling 5,953,323 yuan, resulting in labor costs of approximately 1350 yuan.
- Other Costs: Equipment maintenance costs, quality inspection costs, management costs, etc., allocated proportionally, totaling approximately 500 yuan.
- Total Cost: Raw material costs 3322.61 yuan + processing costs 2000 yuan + labor costs 1350 yuan + other costs 500 yuan = 7172.61 yuan.
Case Study 2: Impact of Different Process Yield Rates and Shell-Making Schemes on Costs
- Process Yield Rate: The higher the process yield rate, the lower the cost per unit cast iron component. For example, when the process yield rate increases from 80% to 90%, the cost per unit cast iron component can be reduced by approximately 10%.
- Shell-Making Scheme: Different shell-making schemes have different impacts on costs. For example, when adopting a secondary surface layer shell-making scheme, the cost per unit cast iron component may be approximately 5% higher than when adopting a primary surface layer shell-making scheme.
IV. Conclusion and Suggestions
The cost accounting of cast iron components involves multiple aspects, requiring comprehensive consideration of raw materials, processing, labor, and other costs. By optimizing raw material procurement, updating production equipment, improving process flow, and enhancing production management efficiency, enterprises can effectively reduce the cost of cast iron components. At the same time, strengthening cost accounting and cost control is of great significance for improving enterprises' economic benefits and market competitiveness.
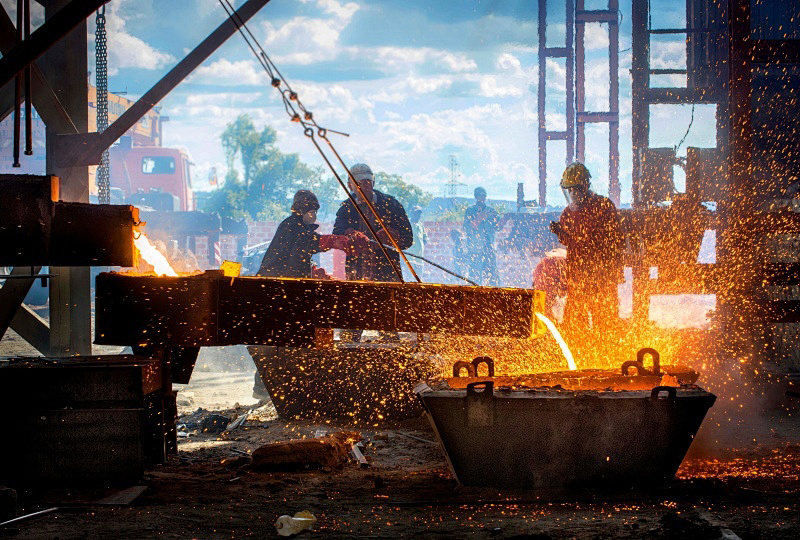