Application of Carbon Fiber Materials in the Automotive Field
2024-12-23 17:38:51 hits:0
Carbon fiber materials, with their characteristics of being lightweight, high-strength, high-modulus, corrosion-resistant, and fatigue-resistant, are gradually changing the face of the automotive manufacturing industry. Especially in applications such as body structures, power systems, and braking systems, carbon fiber materials are bringing about a profound transformation in the automotive industry. This article will combine specific cases to explore the extensive applications of carbon fiber materials in the automotive field and the significant advantages they bring.
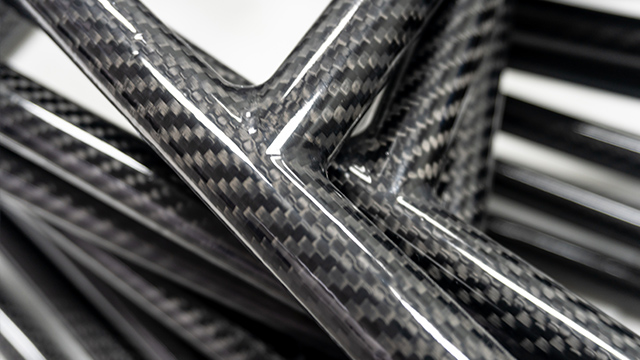
I. Body Structure: Balancing Lightweight and Strength
The application of carbon fiber materials in body structures is a model for the automotive industry's pursuit of lightweight design. The body structures made of carbon fiber composite materials not only significantly reduce the overall mass of the vehicle but also remarkably improve the strength and rigidity of the body. For example, the BMW i3 and i8 models extensively adopt body structures made of carbon fiber composite materials. The carbon fiber cockpit of the BMW i3 achieves a 50% weight reduction, and the carbon fiber body structure of the BMW i8, similar to that of the i3, also realizes significant lightweighting effects. In addition, the Subaru WRX STI TS model uses a CFRP (Carbon Fiber Reinforced Plastic) roof, which reduces the weight by 80% compared to a steel plate. These cases fully demonstrate the huge potential of carbon fiber materials in lightweighting body structures.
The application of carbon fiber materials not only reduces the body weight but also improves the crashworthiness and safety of the vehicle. The tensile strength of carbon fiber composite materials is generally above 3500 Mpa, which is five times that of ordinary steel. The cockpit made of carbon fiber materials deforms minimally during a collision, effectively protecting the survival space of the occupants. At the same time, carbon fiber materials also have a good vibration absorption effect, providing a large buffer against impacts, reducing the generation of impact fragments, and improving the safety of the vehicle.
II. Power System: Enhancing Performance and Efficiency
In the power system, carbon fiber materials are also widely used. Key components such as engine components, drive shafts, and aerodynamic kits have all been optimized using carbon fiber materials.
Engine Components: The high-strength and lightweight characteristics of carbon fiber materials make them an ideal choice for engine components. Carbon fiber intake systems can significantly reduce weight while improving intake efficiency. For example, the Ford Falcon XR6 Sprint sedan adopts an intake system made of 100% carbon fiber, and its intake pipe weighs only 235 grams, while the plastic intake pipe weighs 438 grams. This lightweight design not only improves the responsiveness of the engine but also reduces fuel consumption.
Drive Shaft: Carbon fiber drive shafts have the characteristics of being lightweight, high-strength, and fatigue-resistant, which can significantly improve the efficiency and reliability of the drive system. The carbon fiber drive shaft of the Toyota 86 weighs only 5.53 kg, and compared with the mainstream steel drive shafts, it reduces the weight by 50%. This lightweight design not only reduces the energy consumption of the drive system but also improves the acceleration performance and handling stability of the vehicle.
Aerodynamic Kits: The application of carbon fiber materials in aerodynamic kits helps to improve the performance and fuel economy of the vehicle. For example, the carbon fiber rear spoiler of the Lynk & Co 03 Champion Edition adopts advanced pretreatment processes, molding and curing processes, and coating and quality inspection processes, comprehensively enhancing the appearance and performance of the vehicle. On the highway, the spoiler can efficiently guide the airflow at the rear of the vehicle, reducing wind resistance; in corners, it can skillfully increase downforce, improving the handling stability of the vehicle.
III. Braking System: High Temperature Resistance and High Performance
The application of carbon fiber materials in the braking system also shows its unique advantages. Carbon fiber brake discs have excellent high-temperature resistance and stability and can withstand temperatures as high as 2500 °C while maintaining stable performance. The Porsche 918 Spider adopts carbon fiber brake discs and can reduce the vehicle's speed from 300 km/h to 50 km/h within 50 m. This high-performance braking system not only improves the braking performance of the vehicle but also reduces the energy consumption and wear of the braking system.
In conclusion, the application of carbon fiber materials in the automotive field is constantly expanding and deepening. From body structures to power systems and then to braking systems, carbon fiber materials have brought significant changes and improvements to the automotive industry with their unique advantages. With the continuous progress of carbon fiber material technology and the gradual reduction of costs, it is believed that carbon fiber materials will play an even more important role in future automotive manufacturing.
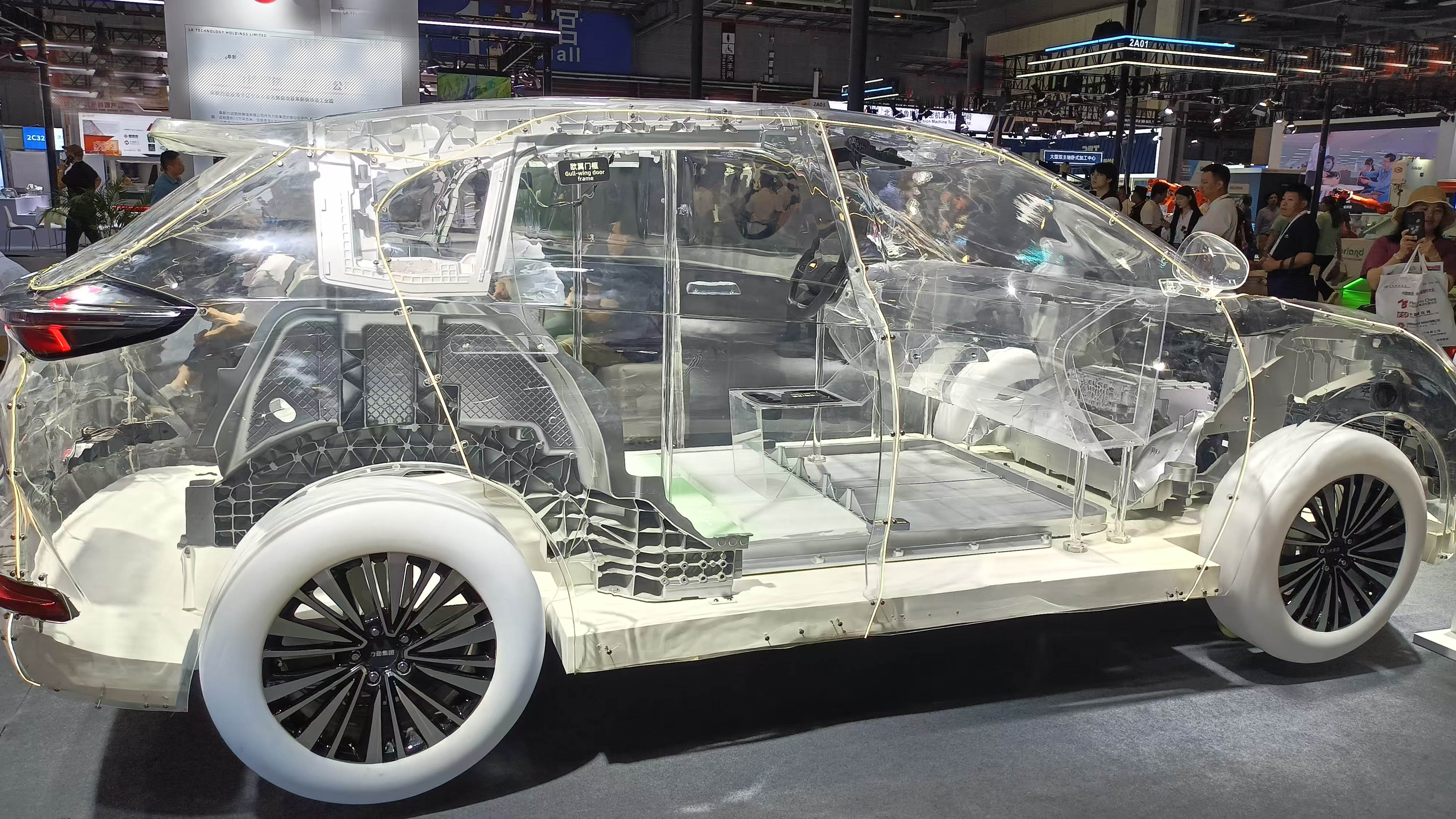