Application of Ductile Iron in High-Speed Rail
2024-12-23 12:06:51 hits:0
I. Application of Ductile Iron in High-Speed Rail
Ductile iron castings, with their excellent tensile strength and yield strength, good impact toughness and fracture toughness, outstanding wear resistance and corrosion resistance, as well as the ability to withstand high loads and friction, are widely used in the production of high-speed rail components.
The axle boxes of high-speed rail bogies, the housings and end covers of high-speed rail traction motors, and the gearbox casings and brake components of high-speed rail trains are all ultra-low temperature impact-resistant ductile iron castings. Generally, they are made of QT400 - 18AL (-50 °C, -60 °C) low temperature impact-resistant materials.
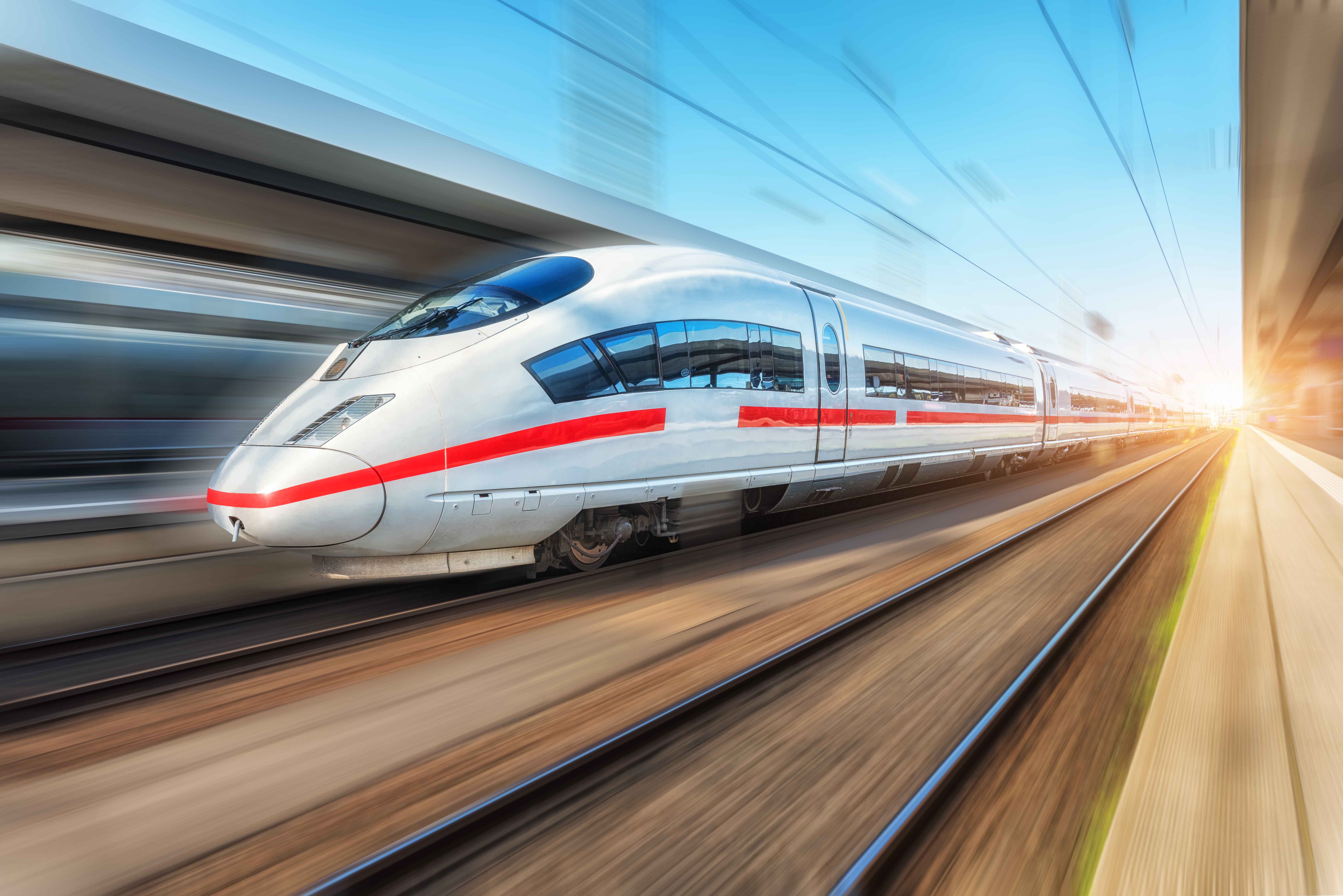
II. Material Standards for High-Speed Rail Ductile Iron Components
QT400 - 18AL (-50 °C, -60 °C) low temperature impact-resistant material, material requirements:
- Material standard: 400 - 18AL
- Tensile strength: ≥ 400 Mpa
- Yield strength: ≥ 240 Mpa
- Elongation: ≥ 18%
- Hardness HBW: 130 - 150
- Low temperature impact value: -50 °C, -60 °C
- Impact energy: 12 J/cm²
- Metallographic matrix structure requirements:
- Spheroidization rate: above 90%
- Graphite nodule count: ≥ 100 nodules/mm²
- Matrix structure: 100% ferrite
- Graphite size: grade 6 - 7
- No phosphorus eutectic and carbide
A 100% ferrite matrix is the primary condition for improving the low temperature impact value of ductile iron. Even 1% - 2% pearlite will lead to a decrease in the low temperature impact value. For ferrite ductile iron, low phosphorus and low silicon annealed full ferrite ductile iron has the best low temperature impact value.
A spheroidization rate of 90% - 95% is a necessary condition to ensure the low temperature impact value. Cracks in ductile iron expand along the nodule boundaries. The rounder the nodules, the less likely cracks will occur. Therefore, the higher the spheroidization rate, the more beneficial it is to the improvement of impact performance and fatigue strength and other dynamic load performances.
The influence of the number of graphite nodules on low temperature impact: A small number of graphite nodules is beneficial to improving the upper limit of impact performance; a large number of graphite nodules is beneficial to improving low temperature impact performance. For axle boxes of bogies with a main wall thickness of 30 mm, 100 - 200 nodules/mm² is appropriate. Phosphorus eutectic and carbide at the grain boundaries will significantly reduce the low temperature impact absorption energy of ductile iron.
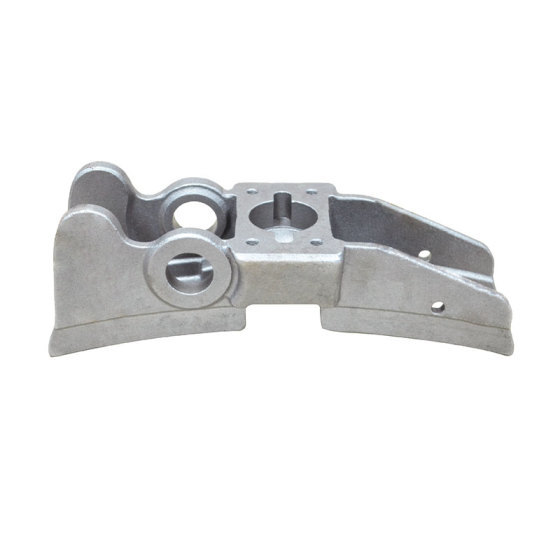
III. Production Process of High-Speed Rail Ductile Iron Axle Boxes
1. Requirements for Raw Molten Iron
Chemical composition of raw molten iron before spheroidization reaction:
- C: 3.9% - 3.98%
- Si: 0.65% - 0.75%
- Ni: 0.75% - 0.83%
- Mn: ≤ 0.10%
- P: ≤ 0.025%
- S: ≤ 0.015%
- Ti: ≤ 0.015%
- Cr: ≤ 0.015%
- Other trace alloys: ≤ 0.01%
The level of Si content directly affects the tensile strength and impact value; when reducing Si cannot meet the strength requirements, the method of adding Ni is used to solve the problem of insufficient strength caused by reducing Si. (Ni is added in this plan)
2. Raw Materials
- Pig iron: Using high-quality pig iron supplied by Tiegu. The total control of trace elements in the chemical composition of pig iron ≤ 0.10%.
- Scrap steel: Carbon scrap steel is used.
- All scrap steel must not be mixed with dirt. Non-ferrous metals or any type of foreign materials, and there must not be excessive rust and corrosion.
- The P and S contents are both not greater than 0.030%.
- The mass fraction of Cr is not greater than 0.1%.
- The mass fraction of Cu is not greater than 0.1%.
- Carburizer: High-temperature fully graphitized carburizer, C ≥ 98.5%, S ≤ 0.1%, N ≤ 0.03.
When formulating the mixture, more raw pig iron is used, less scrap steel and return scrap are used, and the calculation is made to be as close as possible to the ideal chemical composition, leaving a small amount of fine-tuning space. The purpose of adding more raw pig iron is to ensure the number of original graphite cores, and at the same time reduce the amount of carburizer added and the sulfur increase caused by the carburizer. A common formula is that raw pig iron accounts for 88% - 92%, scrap steel accounts for 8% - 11%, ferrosilicon accounts for 1.7% - 2.0%, and carburizer accounts for 0.2% - 0.24%.
- Spheroidizing agent:
- Brand: Lanthanide spheroidizing agent La - 1
- Mg: 6 - 6.5%
- La: 1.0 - 1.2%
- Si: 43 - 44%
- Ca: 2.2 - 2.5%
- Ba: 1 - 1.5%
- MgO: < 0.5
- Granularity: 5 - 20 mm
- Addition amount: 1.2 - 1.3%
- Inoculant: Long-acting composite inoculant is used.
- Primary inoculation: Silicon barium J - 4
- Si: 68 - 70%
- Ba: 4.5 - 5.5%
- AL: < 1.0%
- Granularity: 3 - 8 mm
- Addition amount: 0.8 - 1.0%
- Secondary inoculation: Silicon barium J - 3
- Si: 68 - 70%
- Ba: 2.5 - 3.5%
- AL: < 1.0%
- Granularity: 1 - 3mm
- Addition amount: 0.2 - 0.4%
- Tundish inoculation: Silicon bismuth J - 1
- Si: 70 - 72%
- Ba: 1 - 1.5%
- Ca: 2 - 3%
- Bi: 1.5 - 2.5%
- AL: < 0.8%
- Granularity: 0.2 - 0.7mm
- Addition amount: 0.1%
The inoculant is required to have a strong graphite-promoting effect, can maintain a long time, and has a high and stable absorption rate. Therefore, inoculation is divided into furnace front inoculation, ladle inoculation and tundish inoculation, all of which are indispensable.
At the furnace front, a high-Ba anti-decay, long-acting inoculant is used, and during pouring, a Bi-containing inoculant is used to improve the spheroidization condition in the central part of the cross-section, making the nodule diameter small, the nodule number large, and increasing the ferrite content and improving the as-cast performance.
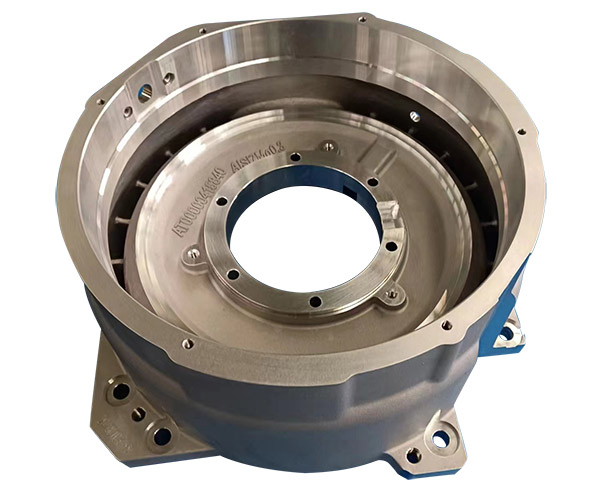
3. Melting Process
The melting process of ductile iron is basically the same. The melting temperature is generally controlled at 1450 to 1520 °C, high-temperature standing, the temperature is controlled at 1520 to 1550 °C, the standing time is about 5 minutes, the tapping temperature is 1480 to 1500 °C, and the pouring temperature is 1420 °C.
After high-temperature standing, when the furnace temperature drops to 1480 °C - 1500 °C, the molten iron is tapped and spheroidization treatment is carried out. After the reaction is about to end, slag is removed 2 - 3 times.
4. Chemical Composition after Spheroidization Reaction
- C: 3.50 - 3.80%
- Si: 2.05 - 2.15%
- Mg: 0.035 - 0.045%
- La: 0.005 - 0.009%
- Ni: 0.75 - 0.83%
- Mn: ≤ 0.10%
- P: ≤ 0.025%
- S: ≤ 0.01%
- Ti: ≤ 0.018%
- Cr: ≤ 0.023%
- Other alloy elements: ≤ 0.01%
Tensile strength: 405 - 415 PMa
Yield strength: 260 - 275 PMa
Elongation: 18% - 23%
Spheroidization grade: 1 - 2
Impact absorption energy: 13 - 15 J
All meet the technical requirements of this brand material.
IV. Key Points of Inmersion Spheroidization Treatment
It must be ensured that the selected spheroidizing agents, inoculants, etc. are pure and free of inclusions, impurities, oxides, etc. These substances cannot be completely removed by slag removal after spheroidization treatment and will eventually enter the casting and cause defects.
- The temperature fluctuation of spheroidization treatment is controlled within ± 15 °C.
- Use a ladle with a dam. The ratio of the depth h of the ladle to the inner diameter ∮: H: ∮ ≥ 1.5 - 2.0 (the actual depth of the molten iron and the inner diameter during treatment).
- After adding spheroidizing agents, inoculants, covering agents and other materials using the dam-type treatment, the dam needs to be at least 20 mm higher.
- The ladles are used alternately. Before use, the ladles are dried thoroughly, and if necessary, they are preheated.
- The packing order is spheroidizing agent, inoculant, and the top is covered with a covering agent or iron filings, which must be tamped to leave no gaps.
- Generally, the optimal reaction time for spheroidization is 1 to 1.5 minutes. Adjust the compactness of the alloy and the thickness of the covering material according to the reaction time.
- The inoculant covering the spheroidizing agent accounts for 40 - 60% of the total (all the inoculants added), the ladle inoculant accounts for 30%, and the tundish inoculant accounts for 10 - 15%.
- The pouring time, from the end of spheroidization to the end, is controlled within 13 minutes.
V. High-Temperature Heat Treatment
To produce QT400 - 18AL (-50 °C, -60 °C) low temperature impact material, the ferrite content of the matrix must be 100%. Since a certain amount of Ni is added to increase the strength, a trace amount of pearlite will inevitably be produced. The purpose of high-temperature heat treatment is to completely convert the pearlite into austenite, and then cool slowly according to the stable phase transformation to achieve the complete transformation of pearlite into ferrite, so as to achieve a 100% ferrite matrix.
Through 870 °C high-temperature heat treatment, there is an impact on tensile strength, yield strength, and impact absorption energy, but there is no impact on elongation. 870 °C high-temperature heat treatment reduces the tensile strength by 5 MPa, but increases the impact absorption energy by 3 J, which can meet the requirements. Therefore, when producing QT400 - 18AL (-50 °C, -60 °C) low temperature impact material castings, an 870 °C high-temperature heat treatment process is adopted.
VI. Precautions
- A 100% ferrite matrix is required to ensure the low temperature impact value, but 100% ferrite is difficult to ensure a tensile strength of 400 MPa. It is necessary to perform solid solution strengthening on its matrix to improve the tensile strength. This requires using a relatively high Si content in the chemical composition or adding alloy elements such as Ni to strengthen the ferrite to meet the 400 MPa requirement.
- The strengthening of ferrite often leads to an increase in the ductile-brittle transition temperature and a decrease in the low temperature impact value. Therefore, it is necessary to adjust the relationship between tensile strength and low temperature impact value, which restricts each other, and explore solutions.
- When the metallographic structure is relatively perfect and basically meets the requirements, to further improve the low temperature impact value depends on the purification of grain boundary inclusions. At this time, how to purify the grain boundaries will be the key factor to ensure the low temperature impact value.
- The impact performance of ductile iron decreases with decreasing temperature, which is an inherent characteristic of ductile iron. To ensure the safe operation of parts at low temperatures, not only the impact value at low temperatures must be ensured, but also the ductile-brittle transition temperature curve, that is, the curve of impact value changing with temperature, must be studied. The flatter the curve drops, the safer it is. A large fluctuation in impact value caused by a slight change in temperature is not advisable.
If you have demands for high-speed rail component castings, you are welcome to contact Tiegu. Tiegu specializes in producing and supplying various kinds of ductile iron castings and gray iron castings of different brands. Our products include vacuum pump valve castings, castings for high-speed rail, agricultural machinery, automotive parts, building materials and so on. We provide global customers with overall solutions and one-stop services for metal forming and processing.Click to view casting products.